By Bahman Azarm,
CEO, The Adventure Parks of Outdoor Ventures
Unless your adventure park is located in a warm climate, the time will come each year when you must close for the season until warmer weather returns. The way you choose to winterize your park can be critical to its success in the season to come.
For our own adventure parks, located in the Northeast and East North Central States, Outdoor Ventures has developed a winterizing technique we refer to as IMP, for “Inspection, Maintenance and Prevention.” For each part of this three-step process, we have specific guidelines that help us assess the park—its equipment, trees, poles and safety aspects—to help us prepare the park for the winter months, use the off-season downtime effectively, and generally prepare thereafter for the new climbing season ahead.
Follow IMP for your park and you will be on your way to having equipment, courses, trees, and operations that will be more efficient, cost-effective, environmentally responsible, and ready to go when it’s time to reopen.
“I” is for Inspections
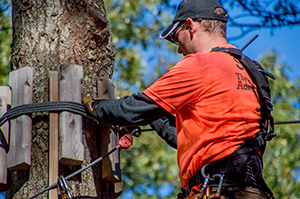
Staff conducting an inspection of the course (photo: Nick Krotki, Outdoor Ventures)
Inspections consist of two tiers: 1) an in-house inspection, followed by 2) a third party inspection.
In addition to your regular, daily, and monthly in-house inspections during your operating season, when preparing for winterizing your park you should perform a final, thorough in-house inspection.
When conducting an this inspection, your aim is to identify any potential issues that may be lurking in your facility and take care of them yourself as needed, before the third party or outside inspector begins his or her work. Some of the things you should include in your in-house inspection:
• tree health or pole condition
• platform condition
• belay/ lifeline condition
• element (or course) condition
• participant equipment
• staff equipment
If you don’t already know your park inside out, this internal exercise will help you get to know it better, so that in the future you can keep an ongoing eye on any issues that pop up, and keep them from recurring during the course of an operating season. By inspecting your park, you may learn things about it that you have thought about previously.
Remember two important guidelines:
1. Always use participant gear when inspecting. Your personal staff gear may allow you to bypass what participants wouldn’t be able to.
2. You are not a good example of the typical participant. Your professional knowledge, experience, and climbing ability is not typical of the average climber visiting your establishment, even if they are frequent visitors. When reviewing our company’s own elements and courses I always try to think and act as if I were a participant, because our courses are designed for their use, not for mine. You can do the same.
In-house inspections allow you to become more familiar with your park’s elements and courses. Knowing what corrective actions and repairs to make before your outside inspector arrives can save both your and the outside inspector’s time, enabling you both to focus on the things you have not already identified and corrected.
And let’s be honest, don’t you want to put your best foot forward before any outside inspector arrives?
Speaking of which, that annual inspection by a qualified third party is required by most states and insurance companies. This inspection will identify issues that you may have overlooked as they accumulated gradually during the rigors and stresses of a season’s worth of use, and gives you time to do repairs. Recommended corrections can be undertaken when there is plenty of time to address all the details, without the inconveniences of doing so during the active season.
“M” is for Maintenance
Maintenance – the repairs and improvements—will be done in two steps as well.
First, address repairs called for by your own in-house inspection. Correct them before the third-party inspector arrives. That way, they will benefit from the outside inspector’s examination and blessing. That provides confirmation that these things were done right.
Second, address any repairs called for by the third-party inspection. The outside inspector will climb the courses, test the equipment, observe the conditions, and so forth. Thereafter, he or she will provide you with a written report specifying what needs to be addressed. These professionals are constantly learning about the latest best practices throughout the industry, and they bring that knowledge to your park’s inspection. Some of their recommendations may introduce you to new ideas; for others, you might kick yourself for missing them yourself during your inspection. In both cases, this is why the industry calls for third-party inspections. Every season and every year, you will learn something new—from both your own inspections and the third-party’s. It’s all good.
In addition, this off-season period of inspections, repairs, and adjustments is an ideal time to make those park or facility additions you may have had in mind, as well.
“P” is for Prevention
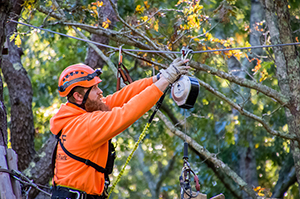
Maintenance team removes an SRL (photo: Nick Krotki, Outdoor Ventures)
The old saying, “an ounce of prevention is worth a pound of cure” surely applies to the ropes course industry. Risk management is all about taking the steps necessary to help avoid accidents or problems in the future. Prevention is also a good watchword for overall operations, whether on the courses, on the ground, in the parking lot, or anywhere else across your facility. Here, let’s focus on the climbing equipment aspects.
Here are some key areas in terms of preventative measures on your courses:
Take things out of the elements (no pun intended):
Getting your equipment and material out of the elements can preserve them and extend their life. (If you were tied to a tree outside all through the winter, you might show some wear and tear, too.) Among the items to bring inside:
• Protective Pads. Remove tree trunk or other pads or cushions so woodland critters are not tempted to nest in or on them.
• Banners
• Signage. Directional or other signage that might be vulnerable to harsh weather should be moved indoors, if practical.
• Hanging Equipment – SRLs and auto belays are expensive enough to begin with. This is a natural thing to do anyway, as you will want to inspect them and have their annual recertification done should it be required.
• Moving Elements. Winter weather can be harsh on rolling and moving elements. Internal mechanisms may be vulnerable to unremitting damp and cold. Moving elements that are left to swing in the wind could become damaged or damage the trees or nearby structures about them.
Once your equipment has been taken down, that is the perfect time to make repairs that you are qualified to do, and to ship devices and equipment back to their respective manufacturer-approved facilities for recertification.
Equipment Storage Tips
You have removed equipment from the harsh outdoor elements for the off-season months. Now, be sure to store them in the right conditions indoors.
• Harnesses should be kept in a dry, cool place, out of the reach of animals and exposure to sunlight.
• Metal equipment should be kept away from water or damp to avoid corrosion. I try to avoid storage in outdoor, non-climatized sheds, as even sealed plastic bins can be chewed through by rodents.
Age-Related Preventive Maintenance
Inspect all your equipment with a critical eye, and retire any that may be past its operational life. If it served you well but is now too worn, loose, corroded, frayed, unsightly, etc., say good-bye and replace it. When retiring lanyards or harnesses, cut them before they are placed in the trash bin, so no one will be tempted to remove and use them. Remember, safety and prevention are your watchwords.
Tree and Pole Maintenance
Don’t forget the trees and poles. For most parks, these structures make our business possible. Make the necessary adjustments in your elements and courses to compensate for tree growth or movement. Poles should be checked for cracking, rotting, and water penetration. Seal and cap as needed. Maintain good tree health and pole condition, and they will go on giving to your courses and your climbers.
Access Prevention
When your park is closed to the public for the off season, make absolutely sure the courses are closed off securely, and that other closed aspects of the facility are locked and inaccessible to uninvited visitors. In addition, it’s a good idea to place “closed, do not climb” signs at all access locations.
Follow these IMP steps, and your park will be well prepared for the following season.