Wire rope is a consumable product, in that it gets “consumed,” or wears down, when in use. Wear needs to be measured and analyzed to determine if the wire rope is still able to function as the designer or manufacturer originally intended it to. Simply put, as the inspector, you must assess whether the wire rope will continue to perform its job before the next regular inspection or maintenance.
Daily, periodic, and annual inspections are required on zip lines, challenge courses, and aerial adventure parks. This article will explore the basics of wire rope inspection in the aerial adventure industry, but it is not a substitute for professional training and on-the-job experience. Your manufacturer/installer should provide you with basic information on wear limits for their products, and how to assess them during your daily and monthly in-house inspections.
For further information, ACCT and NAARSO offer inspector certification that is relevant to the adventure industry. There are many professional trainings and certifications that will prepare you to perform wire rope and other rigging component inspections. Organizations such as the Crosby Group and Columbus Mckinnon offer reasonably-priced trainings all over North America.
Requirements for wire rope inspections can be found in the different industry standards (ANSI/ACCT 03-2016; ASTM 2995; ASTM 770; PRCA; EN15567) and the various regulations of jurisdictions having authority (TSSA; OSHA; state and provincial regulations, etc.). Being familiar with these standards and the requirements for inspections and documentation is an important part of maintaining overall course safety and compliance with standards.
Keep in mind that this article does not cover personal fall protection systems or OSHA/ANSI fall protection policies during the inspection process, but assumes you must be able to reach and see the wire rope during the inspection. The gear and equipment needed to do this slowly and safely requires training to use.
INSPECTION PREP
Before starting an inspection, it’s important to prepare by gathering some information and resources. First, find a copy of the Mil-Cert for the wire rope—many standards and regulations require it to be on file.
The Mil-Cert tells us about the wire rope, including the manufacturer (or who commissioned the manufacturing), the type of metal used in the wire rope’s construction, the lay or style of construction, the type of coating applied to the wire rope, what testing was completed and when, etc. (see example).
This is valuable information that helps you look for what is acceptable and unacceptable when inspecting wire rope in the field. The standards for what is acceptable wear will change based on the wire construction and treatment, as well as how the wire is being used in its particular application (zip line, guy wire, element support, running or moving cables, etc.).
In addition to the Mil-Cert, these tools and materials are also recommended for performing an inspection:
• The Wire Rope Users’ Manual – published by the Wire Rope Technical Board
• tension meter (strand dynamometer)
• caliper
• wire rope wear gauge (S)
• sheave gauges
• cheese cloth
• pencil
• paper
• camera
• binoculars
• magnet
• tape measure
• torque wrench
• swage sleeve go/no go gauge
TAKE A CLOSE LOOK
The following steps can typically be done in any order, with one exception: never put yourself or another human onto a wire rope (lifeline) without basic assurances that the life support system is reasonably safe to do so. Based on the type of wire rope, length, and ability to look at “the other end,” the steps outlined here may need to be completed in a different order.
Look at the wire rope from the ground. Look at the entire length and see if you can identify any bumps, kinks, rust, or deformity. To get a closer look, use binoculars or a zoom lens on a camera.
Look at the wire rope terminations. Are they the correct type and size for the wire rope? Are the clamps or terminations installed correctly? Are they properly torqued? An incorrect cable termination creates a significant reduction in strength and reliability.
Look for wire breaks near the cable termination at the base of the clamp—this is a common spot to find them.
Look for damage caused by moving clamps or replacing clamps and installing them in other areas. When a clamp is moved, a dimple or dent of crushed cable is left exposed, and broken strands can be found in there. This area represents a reason to fail most critical cable systems, since the cable has more damage than it should.
Check the wire rope size using a caliper or wire rope wear gauge. Compare the size of the wire rope you find to the size listed on the Mil-Cert. Reduction in diameter of wire rope is caused by many things, including normal wear and tear that leads to peening or the flattening of the wires, which is typical on the top side of zip line cables, for instance.
Reduction in diameter may also indicate the wire rope is overloaded. Every type and size of wire rope has a catalog listing of the maximum tension allowed on it when in use. This maximum tension is the tension of the cable when loaded with a participant(s) and the design load for a rescue staff, if necessary.
SENSING TENSION
To check tension you will need a wire rope tension meter or dynamometer. This tool is calibrated for the specific wire ropes in use. Professional inspectors should have these tools calibrated for a variety of wire rope sizes, since many can be found in the field.
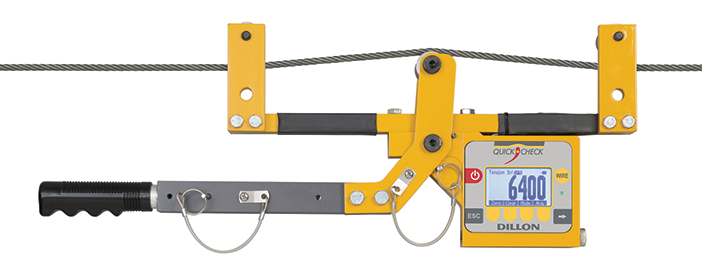
A wire rope tension meter, or dynamometer, is calibrated for the specific wire ropes in use. Use it to measure the standing tension and a loaded tension with a known weight.
When checking tension on wire rope, it’s important to measure the standing tension (no load on the cable) and a loaded tension with a known weight (say, 250 lbs. or more). Document the weight used, as all future inspections should use the same weight. Review the new measurements against previous ones to see if there has been any significant change in the system. A change in tension over a few months or years can tell us various things, but specifically it’s telling us something has changed, and we should examine why.
Many factors can create a change in cable tension, including: initial over-tension of the wire rope; stretch from typical use during the first few months; cable termination slippage; guy anchor movement; pole settling (sinking or shifting) at new installations; or an adjustment to the cable may have been made by other people. You will want to examine the cause, document why the change occurred, and determine whether the cable system is still safe for use, or must be failed and closed until the issues are fixed.
CLAMPING UP
If wire rope clamps or fist grips are used, check the spacing of the clamps (typically 6x the diameter of the wire rope size) and the torque of the nuts on the clamps. Each clamp manufacturer may have a different catalog listing for torque. Many resources exist for finding this information, including the manufacturer’s web page or catalog.
One way to minimize over-torqueing clamps is to use a torque indicator line on the clamp. If the manufacturer didn’t put one on, you can do it. Once a clamp is properly torqued, draw a line down one face of the nut and onto the clamp body or threaded bolt. In the future, you will only need to check that clamp to see if the lines match up.
BY A STRAND
Check for broken strands. Broken strands can be seen with the naked eye in a controlled environment, but are impossible to see while zipping at 35 miles per hour.
So how do you inspect a 300- to- 3,000-foot-long zip line? That’s where cheesecloth comes in handy. Slide the cheesecloth around the wire rope and, holding it tightly with a gloved hand, slide it down the cable during the inspection. The cheesecloth will catch and pull on broken strands. Visually inspect any section that catches, and count the broken wires to determine if they are “crown breaks” or “valley breaks.”
Once you identify the breaks and types, you will need to determine how many broken strands exist in a lay. This is when you pull out your standards and your Wire Rope Users’ Guide to determine if the wire rope is still good to use based on the number of broken strands allowed per lay. If it’s good to use, document the location of the breaks, so in future inspections you can determine if additional wires have broken.
How many breaks are too many? If there are six or more broken wires within one lay, or three or more broken wires in one strand within a lay, the cable should be retired and replaced. Wire ropes work like a machine: when too many parts are broken, the loads get shifted to other parts of the machine, eventually overloading them and leading to failure.

An Inspector using an electromagnetic, non-destructive testing tool to inspect a zip line. He never complains about the view from his office.
A wire rope inspector should also take the time to inspect the equipment being used with the wire, including trolleys, pulleys, and safety hooks. The metal components that ride or travel on the cable are sometimes made of harder materials, and a little nick on the trolley can do a lot of damage to the wire rope over time. Use a sheave gauge to make sure the trolley sheaves are in good shape and are the proper size.
And finally, always document what you’ve done. Take pictures, sketches, and notes. Document the time of day, the location of any damage found, the steps to remediate the problem, and the timeline to complete the work. Document the tools used to make the assessment and the calibration dates of those tools, if applicable.
While safety is everyone’s responsibility when working or playing at height, a large number of staff and guests rely on the inspector to take his or her time and look for minor issues before major issues occur. Being a properly trained, qualified, or competent professional is key to performing this task. Having the correct tools and materials, and the necessary on-the-job experience to make critical safety calls, is essential to get the job done right.
From ANSI / ACCT 03-2016
E.2.4 Inspection and Evaluation: Inspection of both metallic and non-metallic rope used in lifelines shall include an assessment of the entire span, including termination points, operational wear and fatigue points. The designer, manufacturer, and/or inspector shall determine if and when additional non-destructive test methods are required in order to assess the integrity of the wire rope.
E.2.4.1 A wire rope lifeline shall be retired from service when any one of the following occurs:
• The reduction in nominal diameter due to tension, wire breaks, surface wear, metal loss, or corrosion amounts to 5% or more from the diameter measured under tension at commissioning.
• The crown (surface) wires are worn by approximately 1/3 or more of their diameter.
• There are 6 or more broken wires in one lay.
• There are 3 or more broken wires in one strand in one lay.
• There are 1 or more broken wires within one wire rope clip diameter of an attached fitting due to fatigue.