Inspection of fiber ropes is one of the most important jobs at any aerial park or ropes course. The condition of your life safety ropes—belay lines, lanyards, evac and rescue ropes, and even ropes that support elements at your operation—directly impacts the safety of your guests. However, inspecting these ropes is not the most fun job, and is often done begrudgingly, at the end of a long day or early in the morning before one.
Rope inspection deserves your full attention. Visitors entrust you with their lives on a daily basis, and your goal must be a 100 percent success rate. To accomplish this, the quality and condition of the ropes you use is one of the top factors in making sure everyone gets to the ground safely.
Having spent 25 years working in IT management, I know that a 100 percent success rate takes effort to achieve. The gold standard for the availability of any good IT system is 99.999 percent uptime, and that is rarely achieved. That same level of success in the aerial adventure park world, though, would be disastrous: one out of every 100,000 participants would not make it home.
Modern life-safety ropes are highly engineered tools designed to defy gravity with the least amount of impact to the user. For the most part, ropes are built for use in a specific situation. Many factors determine the performance of these ropes: the type of fiber used to make the rope, the amount of twist used in the rope, and the construction of the rope. In this article, we are going to assume that you are well aware of the types of ropes used in your specific applications, and that you have chosen the proper ropes for each use.
Over time, even the best ropes will gradually begin to deteriorate and lose some of their initial qualities. Eventually, this will reach a point where the loss is great enough to warrant retirement of the ropes. The maximum life span for life safety ropes is ten years from date of manufacture, or five years from the date of first use—whichever comes first.
Remember, that is the maximum life of a rope. Some need to be retired earlier, and inspection is the only way to know when a rope’s performance has been impacted to the point where it needs to be replaced.
The ANSI/ACCT 03-2016 standard leaves a lot of decision-making authority in the hands of the person performing the inspection. To guide your efforts, let’s dig into the specifics of the process.
KEEP TRACK
The first step is to establish procedures and retirement criteria by which the ropes will be measured. These will vary: they are based on the activities the ropes are used for and the types of ropes used.
To start, it’s best practice for rope inspections to be performed before and after each use. The procedures for inspection must be site specific and written by, or following the advice of, a knowledgeable and qualified person. Once procedures have been established, the qualified person should then train the staff who will be performing the inspections so they know what to look for, how to look for it, and what to do if they find an issue.
Tracking is done by compiling a “rope log.” Most rope companies include a version of a rope log with their user instructions, but if not, your friend Google can help you find a template rather quickly. A good rope log will include ways to identify the rope (manufacturer, type, diameter, length, lot number, or other specific ID), the manufacture date, the date it was put into service, and any fabrication that was added to the rope (splicing, sewing, hardware, etc.).
In addition, there should be a line-by-line inspection and incident history of the rope. The inspection portion should contain a line for every inspection, and everything of note that was found during the inspection (if anything). The incident portion should note any potentially damaging events, such as major falls, high abrasion situations, significant environmental factors, etc. These rope logs should be maintained religiously throughout the life of the rope. They are a major safeguard for your business in the event of an incident.
TAKE A CLOSE LOOK
Now, the fun part: performing a thorough inspection of every inch of the rope, by section. To do this, pull an arm’s length of the rope with one hand, while keeping your dominant hand on the rope and feeling it as it pulls through. This is called a tactile inspection. Note any anomalies: high spots, stiff sections, hard spots, glazing, low spots, changes in diameter, sheath damage, etc. You should be able to feel any of these. If you find any issues, perform a full investigation to find the cause of what you felt, and determine if the rope should be retired.
If the tactile inspection doesn’t produce any issues, perform a visual inspection of the same arm length. While holding the rope under manual tension, look down the length of it, similar to the way you might inspect a pool cue to see if it is straight. The first thing to look for is any change to the pick length (for kernmantle or braided ropes) or lay length (for twisted ropes) in the rope. The pick length and lay length are natural patterns made when creating the rope. You should ignore the colors in this step, and focus on the construction. Any changes, or “cork screwing,” could indicate areas of damage. Be sure to look over all sides of the rope.
Next, look at the color pattern and overall condition of that same section of rope. Keep an eye out for divots, cuts, heavy abrasions, glazing, high or low strands, changes in diameter, fuzzy yarns, etc.
Perform these two visual inspections in separate steps. That way, you are twice as likely to catch an issue. You don’t want to try and focus on too many things at once. As with the tactile inspection, always fully investigate any issues and determine whether to retire the rope or move on.
You should also inspect any fabrication (splices, sewing, and/or other components and manipulations) as you come across it. Look for rusted, cracked, or worn hardware, loose connections or splices, tears and any other notable concerns. These connection points are as critical to your systems as the rope itself, and should be given the same level of attention.
If a section of rope passes inspection, move on to the next arm length, and so on. If no issues are found, great! Have full confidence that your rope is ready to perform as intended.
If you find areas of concern and want another qualified person to inspect it, mark the areas with a brightly colored piece of electrical tape wound tightly on each end of the issue. Obviously, the rope should be kept out of service until that second inspection takes place.
WHAT TO LOOK FOR
The following are a few of the issues you may find, along with possible causes.
• Shock loading, chemical exposure, and excessive tension. Each issue can significantly reduce the performance of a rope, either suddenly (in shock loading or chemical contact) or over time (in excessive tension usage). Often, these issues can only be found by inspecting the rope’s log.
• Hockling, twisting and cork screwing. These are examples of damage to the construction of the rope, and a telltale sign that the rope has been shock loaded.
• Cuts. These are the most serious area of concern. A cut indicates loss of strength and/or exposure of the core yarns. Ropes with cuts should be retired immediately. Inspect all hardware and edges in the system to identify and eliminate the root cause of the cut to prevent a recurrence.
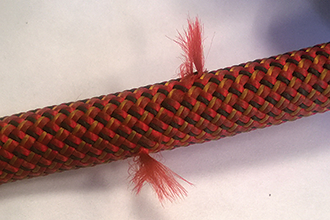
Evidence of broken fibers in the rope, which can often occur during normal use.
• Abrasion. This is evidence of broken fibers, which often occurs during normal use. It’s important to determine when the number of broken fibers will materially impact the strength of the rope. We have tested heavily abraded ropes, with a resulting strength loss up to 80 percent, that were still in use.
Kernmantle ropes are more likely to abrade on the outside of the rope; twisted ropes will abrade both on the outside and between the strands, where the strands rub against each other, since there is no protective sheath.
• Bumps in the rope. These typically indicate areas where the core yarns have kinked up inside the sheath. Since kinked core yarns can cut though each other with relative ease when put under tension, this is a serious issue.
• Soft spots or depressions in the rope. These are direct indications of damage to the core, usually broken core yarns. These defects should warrant immediate retirement.
• Glazing. When the surface of the rope becomes hard or black, this indicates melted fibers, a significant concern. In minor cases, black coloration indicates wear and high tension or sharp bends in the use of the rope. Hard, melted sections are a greater concern. Inspect the overall system, and add shear reduction devices or any other means of reducing the damage. This issue will also occur in highly repetitive rappel ropes that are subjected to heat through the friction with the descent devices. It is fairly normal, but can be avoided by frequently changing to a “cool” piece of hardware.
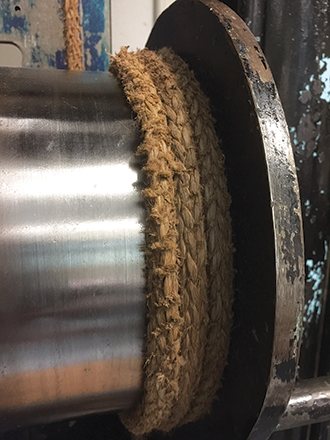
Excessive wear on the rope fibers can be caused by dirt, glazing, or over-use, among other factors
• Dirt. Grains of sand/dirt will create excessive wear on rope fibers. Dirty ropes should be washed as per the manufacturer’s instruction.
REACHING RETIREMENT
When you find a rope that should be retired, cut it into smaller sections to make sure it does not accidently find its way back into use. For a longer belay or evac rope, cut it into 20-foot sections and use these for knot training, fencing, or elements where the rope is not relied upon for the safety of others.
Make inspection a regular part of your program, always thoroughly train every new employee (including temporary workers) how to inspect ropes, and keep complete rope logs. When it comes to inspecting ropes, there’s an old adage that’s still relevant: “When in doubt, throw it out.” Or even better, recycle it for some good karma points.
For more information
This is an abridged version of the procedures for inspection and the causes of failures. Your rope manufacturer or the Cordage Institute can supply more detailed information. The institute has a detailed guide to fiber rope inspection, the Cordage Institute International Guideline for Fiber Rope Inspection and Retirement Criteria (CI 2001-04). You can read the standard at www.ropecord.com. The guideline has been developed by some of the most knowledgeable rope experts.