At some point, to paraphrase the great B.B. King, the thrill must be gone—or at least come to an end. After the heady rush of soaring through the air on a zip line, a rider must come to a safe stop. That makes brakes a fundamental component of any zip line installation. And there are many ways to slow a rider down, for both speed control during a ride and for the complete stop necessary upon arrival at the end of a ride.
Braking systems achieve speed control through a variety of means: friction, elasticity (or compression), magnetism, electricity, or the pull of gravity. Depending on the specific application, designers and builders have options.
Among the variables to consider are line length, gradient, line tautness, weather, and traffic volume. Budgetary restrictions and maximizing throughput are considerations, too. It takes a carefully designed system, not just a well-designed device, to provide appropriate and safe zip line braking.
The components of a brake system can include prussiks, brake blocks, spring banks, magnetic eddy-current devices, and more. Course designers can choose from this suite to meet the specific needs of the landing zone. Standards adopted by an authority having jurisdiction (AHJ)—or, in cases where there is no regulation, by the designer—can, of course, dictate the details of how a brake system must operate as well. While the ASTM, ANSI/ACCT, and ANSI/ PRCA standards differ in many details, they have a common goal: that a brake system must bring participants to a safe stop, even in the case of a complete primary brake failure.
With a few exceptions, such as gravity brakes, many zip lines require both a primary and backup brake system to meet that goal, given the arrival speeds of many longer lines at recreational/ commercial operations. Typically, these backup systems—or emergency arrest devices (EAD), as they are frequently called—must be fail-safe or involve a redundancy that makes them effectively fail-safe (redundant systems are unlikely to fail at the same time). Some systems include three or more braking strategies in an integrated system.
And finally, for park operators or builders contemplating a braking upgrade for an existing zip line, there is the issue of compatibility—making sure that all braking products and components, new and pre-existing, work together seamlessly. (See “Upgrading Safety Systems,” p. 38, for more.)
MECHANICAL SOLUTIONS
For backup or emergency systems especially, it’s important to remove guide or rider involvement from the braking system. That makes mechanical systems essential. These can include things such as spring packs or the “counterweight progressive brake” that Zip-Rush principal Stephan Bernier likes to use for high-speed landings. They also include any of the more sophisticated mechanical components that suppliers have developed.
Let’s look at several of these:
zipSTOP. Head Rush’s zipSTOP system is perhaps the braking methodology of choice for high-volume commercial parks, where Head Rush “has its home,” according to Rich Reynolds, VP of engineering and products. Braking is produced by magnetism in its eddy current system as aluminum rotors expand into a magnetic field within the braking compartment to slow riders down. ZipSTOP can be used as either a primary braking system, an EAD, or both.
A key to zipSTOP’s popularity for high-volume applications is automation. The brake automatically adjusts to rider weight and speed, and automatically resets after each run. That means guides can get the next rider on the line quickly, with no adjustments necessary. That can be an important consideration in jurisdictions that require the EAD to reset automatically.
At several thousand dollars apiece, zipSTOP units aren’t inexpensive, but the extra cost is often offset by higher throughput. Because aluminum is a non-conductive material, heat-related wear and tear is not really an issue, says Reynolds. However, annual maintenance by Head Rush is required to be sure the units continue to function properly.
Zipkea. Of the various mechanical systems on the market, one of the simplest is Hackwell’s Zipkea brake, which can be used as either a primary or backup brake. As a primary brake, it can also be used in conjunction with Hackwell’s Autoprusik EAD.
The Zipkea unit is an octagonal cylinder that surrounds the zip cable (any half-inch line, according to Hackwell’s Tommy Cooper). An approaching trolley or carabiner is captured by the Zipkea, and the kinetic energy produced by the rider is absorbed by the wheels inside the unit, slowing the rider to a stop. The braking force calibrates automatically according to the rider’s speed and weight. The Zipkea comes in two versions—an eight-wheel model for average speeds in the 15-20-mile-per-hour range, and a 12-wheeler for higher speeds.
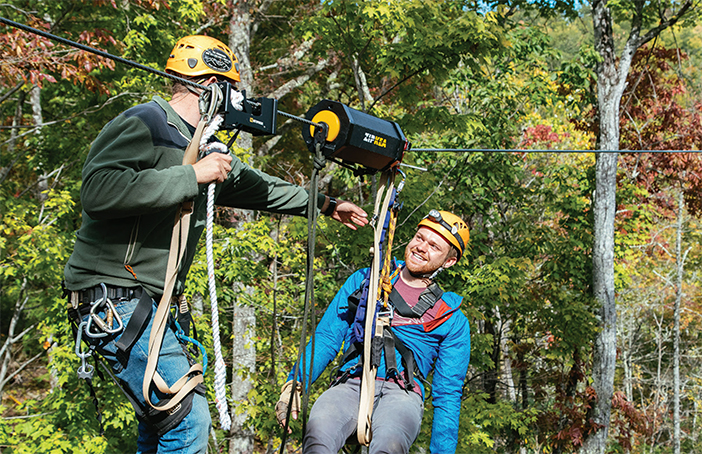
Hackwell’s Zipkea can be used as a primary or backup brake, and is designed for negatively sloping lines.
There are limitations, however. Cooper says that the Zipkea is “designed for negative-sloping lines,” meaning that, due to the catenary, or belly, in a line, riders are already losing speed by gaining elevation as they approach the terminus. Hackwell’s website suggests that the system can also be used for some flat or positive-sloping applications as well. The Zipkea comes equipped with a retrieval line for slower approaching riders who might come up short of the landing platform.
According to Cooper, other than daily inspection, the unit requires relatively little maintenance given that “the polyurethane wheels have a long life span.” A prominent Zipkea user is ClimbWorks, with the system in play at its installations in Gatlinburg, Tenn., and Oahu, Hawaii. Both sites have high visitation rates, and high throughput is at a premium.
Hackwell’s Autoprusik EAD simply transforms a normal prusik into a passive system that requires no action from a guide. The stopping power can be adjusted to suit the requirements of the arrival speeds and the landing zone.
Bonsai Emergency Arrest System. Bonsai Design is an all-in-one-package adventure-park company—a designer, builder, operator, inspector, trainer, and equipment designer. Bonsai offers several emergency braking components, primarily the Emergency Arrest System (Brake Bobbin, EAD, All-Stop) and the zip E-Brake, which are often combined with Head Rush primary braking systems. The typical configuration has a Head Rush zipSTOP installed as the primary brake, with a Bonsai EAD as backup. Bonsai’s John Nixon touts relative simplicity as a selling point: simple mechanically, simple to install and operate, and simple, relatively speaking, on a park’s pocketbook. That said, he adds, “We do require professional oversight of the installation of our systems, which includes testing and associated documentation.”
The Bonsai Brake Bobbin acts as a capture device for a variety of trolleys, according to Nixon, making it a sensible choice for retrofitting an existing zip line. The company’s EAD, a five-foot-long padded device/mechanism attached to the cable, also acts as a capture device to facilitate turnaround and increase throughput. When combined with Bonsai’s All-Stop, the Brake Bobbin and EAD package become a fully integrated emergency braking system.
The company’s zip E-Brake is primarily designed for use in courses with smaller operational space in the landing zone. The zip E-Brake may be installed with an automated counter-weighted return system to create a fully automated emergency brake system.
Switchback. One of the more interesting technologies to enter the zip line braking market is the Switchback, a new electrically-controlled system developed by Holmes Solutions, due at press time to hit the market by the end of 2021 through Ziptrek Technologies. Holmes, a New-Zealand-based engineering company, has a portfolio that covers several industries, including transportation, construction, and recreation. NASA is one of its clients. While its new braking system might not come from the realm of rocket science, it’s in that orbit.
Switchback is designed for installations that combine zip line and curved rail segments, making speed control, specifically at the transition points from rail to zip line and back, a particularly critical component of a tour’s overall configuration. Although Holmes’s Dan Brennan says the new braking system is designed for zip-rail combinations, it is conceivable that it could be used for a straight zip line tour.
The braking component in the Switchback system is incorporated into the trolley, which is “pre-programmed with a set of velocity profiles,” according to Holmes technical director Ben Woods, allowing the operator to choose a speed profile for each individual rider. Because the non-lithium battery in the trolley “regenerates on the way down,” according to Woods, any concerns about losing the electrical charge are minimized.
Brennan concedes that the Switchback will come with “a higher price tag” compared with other trolley/braking systems, but he contends that higher throughput—“hundreds of people per hour”—can offset the higher cost. In addition, he says, the efficient operation of the system “shaves down manpower.”
PASSIVE VS. ACTIVE BRAKING
Does the Switchback design, as the newest concept to hit the market, represent the next step in a general trend toward passive, automated braking systems and away from old-school active braking systems, especially for pay-toplay operations?
Brennan, for one, believes so, saying “it is probably happening on a stretchedout timeline, but yes, it’s happening.” Bonsai’s Nixon concurs. The recreational industry, he says, “is moving away from manual, participant/guide-facilitated braking systems.”
But not so fast. Hand braking still has plenty of proponents, in both the recreational and educational realms. Bonsai itself recently installed a system with hand-braking as part of the primary braking system for the Telluride Canopy Adventure in Colorado. “This allows for a more dynamic participant experience,” as Nixon notes.
ZipTour. Consider Terra-Nova’s ZipTour active braking system, with which riders control speed by a hand-operated lever that applies or releases pressure exerted on the cable by a brake pad. Terra-Nova has made active speed control a major selling point. Riders, if they so choose, can achieve speeds of 65 miles per hour or more, or stop mid-span to enjoy the view, depending on the length and gradient of the line and a rider’s need for speed.
Terra-Nova owner and founder Eric Cylvick calls the technology “established and mature,” meaning that it has proven its reliability over time as well as in especially challenging environments. The company installed one of the world’s longest zip lines, at 8,350 feet, in Copper Canyon, Mexico (where zip speeds of up to 84 miles per hour have been touted). Another installation, on St. Martin in the Caribbean, has a gradient of 43 percent, according to Cylvick. Long and steep rides “are our niche,” he says.
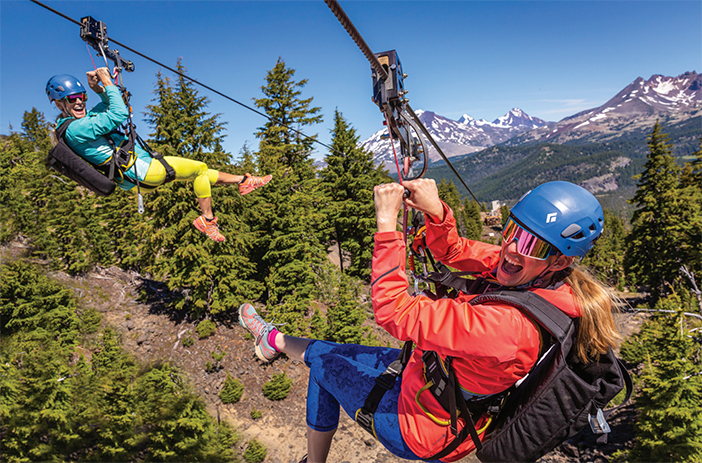
Terra-Nova’s ZipTour trolley involves an active braking system that is controlled by the rider with a hand operated lever.
Active speed control suggests a heightened need for a bulletproof EAD incorporated within the overall braking system; Cylvick says something as basic as a graduated spring stack—“reliable and low-maintenance”—can accomplish that mission.
When it comes to maintenance, Cylvick says the system is “super-reliable,” and although friction, which tends to generate heat, produces the braking force, the brake pads are made of a non-conductive material, resulting in little heat and thus relatively little wear and tear, he says.
FINAL CONSIDERATIONS
Within the broad array of braking products available, and hence the choices a park builder or operator needs to sort through, there is not necessarily one braking system that works better than another. The choice isn’t based on inherent effectiveness; all proven braking systems are capable of bringing riders to a safe stop. The specific parameters of an installation are the deciding factor. What works for a gently sloping zip line, for example, might not be the best solution for a long, steep ride.
Key factors. Basic design considerations—line length and gradient, the speeds involved, landing zone length, traffic volume, etc.—obviously come into play, but so do operational considerations, including throughput maximization and clientele assessment. Some park guests, for example, might relish the opportunity to achieve max speed with a ZipTour system. At another park, the majority of guests might prefer the micromanaged control provided by the Switchback configuration.
And, of course, there are always budgetary considerations, and spending more on a braking system doesn’t necessarily translate into an increase in safety or effectiveness. For certain installations— where speeds might be lower, transition points fewer, visitation rates lower, etc. —a relatively simple, relatively inexpensive, and relatively low-maintenance system might fill the bill.
Compatibility. Obviously, zip-line braking technology has evolved over the last 20 years, and continues to evolve. None of the manufacturers except for Switchback/Holmes have introduced any major changes to their braking lineup, but small evolutionary tweaks happen frequently. Over time, each incremental change has to be accounted for. A Zipkea capture device, for example, might not work well, if at all, with an older trolley.
Some braking products are specifically designed to be compatible with products from another company. Bonsai, for example, has designed components that work hand-in-hand with Head Rush’s zipSTOP. On the other hand, something like the Switchback’s new electrical system is fully integrated, and thus presumably incompatible with another company’s components.
The thrill of zip lining comes from the sense of freedom, excitement, and abandonment produced by virtual flight. Braking, or speed control, represents something almost antithetical. It is possible, of course, to provide a thrilling experience that ends with a controlled landing. In choosing a braking system, a builder or park operator needs to determine, depending on the nature of the ride and the clientele, where the ideal balance between thrill and control lies.