The zip line trolley is such a simple piece of hardware, yet every day it seems to grow increasingly more complex. It is one of the most critical components of a zip line system, and its influence reaches well beyond its main job. A site’s zip line trolley choice affects cable replacement cost and frequency, brake system choice and performance, and maintenance costs. It also affects systems compatibility and overall design, rider throughput time (tour length), operational burden, and, most importantly, rider experience and safety.
The list goes on—including noise ordinance compliance, oddly enough—and all these impacts have fueled a great deal of innovation in what is, at heart, a simple piece of equipment. Those innovations include several that are beyond the scope of this article, such as system-specific trolleys like the ZipRider from Terra-Nova, and zip rail coaster trolleys like the Holmes/CLIMB Works Switchback and Walltopia Rollglider. Here, we’re focusing on standalone trolleys operators might choose to upgrade their current equipment, without other major modifications to their system or operation.
So let’s take a look at the innovations manufacturers are making, and ponder some of the characteristics to consider when researching which trolley to purchase next. It is often a large investment, so make sure you have the information needed to make an informed decision.
With so many options, though, choosing which trolley will best suit your current or future operation can be complicated. I spend a great deal of time deliberating equipment choices for various operations, and I assure you, there is no one-size-fits-all solution.
INNOVATIONS
Integrated-connector trolleys. One of the most prevalent innovations is the carabiner-less trolley, otherwise known as an integrated-connector trolley. By eliminating the lanyard-to-trolley-carabiner connection, manufacturers can eliminate multiple issues, including failed carabiner gate closures and wear points due to use of dissimilar materials, and also add new features, such as easy, one-hand operation for guides or operators.
Trolleys featuring this style of closure are often more expensive than those with a carabiner connection. But the ease of operation, simplicity of the system, and overall style make the feature worth checking out.
Manufacturers currently offering an integrated-connector trolley include Kong, Koala Equipment, Head Rush Technologies, ISC, and Petzl.
Brake-friendly and impact-friendly trolleys. The innovation here involves the leading edge of these trolleys and how they interface with the various zip line brake systems available today. For Head Rush, for example, this innovation is critical, since it is a manufacturer of both trolleys and zip line brake systems. It has designed a flat, non-metallic leading edge to all its trolleys. This ensures the interface with the braking system is smooth and non-damaging, resulting in extended life of both the trolley and the brake system.
Other manufacturers, including ISC, are addressing this zone of the trolley in various ways. But the common theme includes non-metallic materials and field serviceability. As speeds increase on zip lines and brake systems become more prevalent—not to mention critical—this innovation will grow in demand and importance.
Head Rush is also addressing what it has coined as “the overturning moment.” This occurs when the trolley does a wheelie on its rear wheel as the trolley slams into the brake system and the zip line rider swings up. This causes more wear and tear, because the wheelie motion and position often cause the trolley body to rub on the cable at a high speed, while introducing additional friction into the system.
If this action occurs only rarely—an emergency stop, for example—it is not a big deal. But when this action occurs multiple times a day, the trolley body will wear quickly, and it will cause significant damage to the cable over time.
Head Rush addressed this issue through two different designs: one has a pivoting attachment link, the other, a forward-of-center connection point for the rider. More manufacturers are beginning to pick up on these nuanced design details as sites begin to demand longer-lasting, brake-friendly trolleys.
Field-serviceable trolleys. These trolleys allow the owner/operator to replace wear-and-tear parts with OEM parts at their own discretion, without the need to ship the trolley out for service when parts need to be replaced. This offers massive cost savings, is much smarter for manufacturers, is more environmentally-friendly by reducing waste and reusing valuable parts, and should be high on the list of critical features for your next trolley.
Integrated magnetic brakes. Ultra-premium zip line system and equipment manufacturers are integrating magnetic trim-brakes into zip line trolleys. The purpose of a trim-brake is to reduce the overall top and average speeds on a zip line, thereby allowing steeper zip line designs. This innovation opens a world of possibilities for zip line locations previously considered impossible or too dangerous, while also helping existing operations ensure their brake speeds are within the manufacturer-specified parameters.
While this technology is promising, early iterations have struggled with adequately dissipating the build-up of extreme heat. However, a next-generation design from recently-formed Xtreem Ziplines (see “IAAPA report,” above), currently in the prototype stage, is proving successful in decreasing heat build-up and allowing end users to easily tune the trim-brake force to account for variations in user weight, zip line designs, and environmental conditions. Keep an eye on this area of innovation, as it is poised to deliver an advantage that every operation can leverage for a safer user experience.
Polyurethane wheels. Most sheaves (i.e. wheels) are constructed from a steel-alloy material, but an innovation becoming more readily available is polyurethane wheels, which have more dynamic properties than the standard steel-alloy options. Rollercoaster wheel manufacturers, including Uremet and Millennium, have started producing polyurethane-based wheels for ultra-premium trolley manufacturers.
With the new polyurethane technologies, these companies are able to modify the hardness (i.e. durometer) of the tread material, which in turn influences the speed and durability of the sheave. For example, a softer tread will run slower, have a lower heat tolerance, and have a shorter lifespan due to wear than that of a harder wheel, which will run faster and have a longer overall lifespan due to better temperature performance.
As zip lines grow increasingly more complicated, designers are considering these factors more often and, in some rare cases, even beginning to specify “winter” and “summer” wheels with varying polyurethane compounds. As an added benefit, using polyurethane sheaves completely eliminates “crowning” on cables, which is the result of wear from traditional steel-alloy sheaves.
New Trolley Tech Debuted at IAAPA
A couple of innovative trolleys debuted at the IAAPA Expo in Orlando, demonstrating our industry’s innovation amid the show’s more typical rollercoasters, VR zombies, and Beaver Tails.
France-based Xtrem Aventures Group showcased a new trolley prototype from Zip-Rush, the Mach II. Noteworthy details: It is constructed with aluminum side plates containing three attachment points and cooling vents near the wheels; has field-replaceable parts, for ease of service; utilizes magnet-equipped wheels to induce eddy-current for continuous trim-braking; and a metal fin provides compatibility with the zipSTOP Brake Trolley catch mechanism. While still in development, first impressions are promising. (Bonus: The booth displayed a prototype harness from paragliding-harness manufacturer SupAir.)
A new company, Xtreem Ziplines, prominently displayed the X2 Trolley. Xtreem Ziplines is headed by three zip line industry veterans who are making a big statement with their first piece of equipment. Visually, the X2 is a major departure from traditional trolleys: it is easy to see how its form follows function. And there’s a lot of technology to see. The X2 features onboard adjustable magnetic trim-brakes, massive heat sinks for radiating heat away from the wheels, polyurethane wheels with a deep v-groove, and ingenious spring-loaded clips to prevent trolley derailment. It also has a handlebar and spreader bar, and built-in integrations for soon-to-be-released brake trolley catch mechanisms and a launcher. Plus, all the trolley parts are field-replaceable.
Two innovative trolleys unveiled at the IAAPA Expo: (left) Zip-Rush Mach II trolley, distributed by Xtrem Aventures Group; (right) Xtreem Ziplines X2 Trolley.
Honorable mention goes to Skyline Ziplines (Whistler, B.C.), a longtime IAAPA exhibitor and zip line manufacturer, for its updated magnetic trim-brake version of the Rocket Trolley. The update focuses on revised polyurethane wheels with improved temperature shedding and tolerance dynamics. Skyline is offering retrofit upgrades for existing Rocket Trolleys and has a field kit for approved sites to install the retrofits themselves.
CHALLENGES
Cost and durability. These are the two big challenges facing the manufacturers I spoke with. Cost and product longevity are two factors at odds with each other due to various considerations, such as ease of operation, small manufacturing quantities, and performance criteria. There are trolley options available at both ends of the price-and-durability spectrum. Economical options often fall short in high throughput and high-speed operations; expensive options that last a long time are often financially unobtainable for many businesses.
Finding the balance within this spectrum is further complicated as engineers, designers, and site operators look to solve more complex zip line system challenges or suit wider operating ranges (i.e., speed and rider weight) with zip line trolley technologies. The challenge here, aside from cost and longevity, is designing a universally applicable, fail-safe solution that does not introduce further room for human error—selecting a special trolley, adjusting trolley settings, etc.—which is the leading cause of zip line incidents.
DESIGN AND SYSTEM CONSIDERATIONS
There are a few basic considerations when choosing a trolley.
Cable size. One of the first filters to apply when deciding on a trolley is considering the cable size parameters for which the trolley is intended. In the past, cable size has not been an issue, as the standard sizes for cable were 3/8” or ½”, but we are now seeing systems with 5/8” all the way up to 7/8” diameter cables.
Trolley manufacturers are responding to this shift in a few ways, including size-specific sheaves, and specifying multiple size ranges for a trolley, with a minimum and maximum cable size. It is important to never exceed the maximum cable size, as this may result in negative consequences.
Speed. The maximum speed of a trolley is a consideration as more sites push the speed envelope. Three factors are instrumental in determining the maximum rated speed: durability and heat tolerance of the sheave material, bearing rating, and trolley body design.
As discussed earlier, the hardness rating (durometer) and heat tolerance of the material a sheave is made of can greatly influence the overall speed of a zip line trolley. The hardness factor impacts the overall speed of the trolley on the system due to rolling resistance, while the temperature tolerance determines the range of speed in which the sheave can operate. Some polyurethanes may only be rated for a specific maximum speed sustained over a definite distance or rolling time before encroaching on the material’s melting point.
The rating of a bearing and its overall quality can span a wide range—a less expensive bearing is an easy cost-savings choice for lower-speed applications, but more demanding applications require a performance increase to address higher maximum speeds, increased running temperatures, and greater cycle use counts. For these advanced performance needs, quality, name-brand, sealed ball bearings are essential. It is important to note that bearings are very different in design from bushings, which are not appropriate for any zip line applications.
Lastly, the trolley body design can influence its maximum speed, based on how it allows the heat from the wheels and bearings to dissipate (or not) and what crash force or speed the body and its components are rated to. And the aerodynamics of the trolley body can also impact the maximum speed.
Braking. As mentioned earlier, the style of braking and design of the braking system have a dramatic influence on a manufacturer’s trolley design, and on which designs are appropriate for a given operation. Without belaboring the ideas of “the overturn moment” and brake-rated front plates, make sure that the trolley designs you consider are compatible with your braking system in terms of functionality, brake impact force, and overall application.
Connection and closure styles. It’s important to consider the various connection methods and trolley closure styles for equipment and systems compatibility, ease of maintenance and inspection, and overall preference. For some, it will be an integrated system with a “direct to lanyard” connection method, which reduces the number of components and therefore shrinks inspection time, inventory of on-hand maintenance parts, and risk of dropped components on course. For others, it will be the more traditional setup of combining individual components to create a custom assembly tailored to their needs and preferences.
Make sure your equipment choices suit your site’s long-term needs, system compatibility requirements, and guest experience.
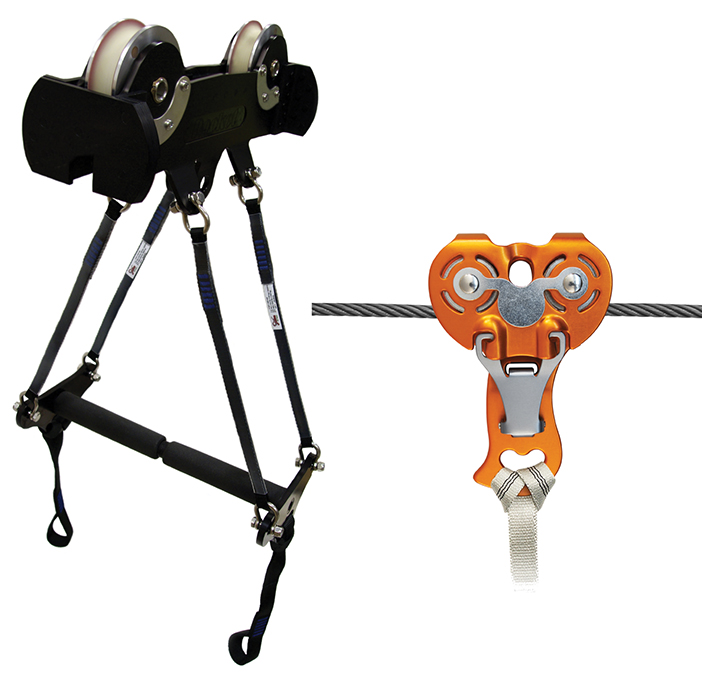
Left: The updated SkyTECH Rocket Mag Trolley, from Skyline Ziplines. Right: The Kong Zip Evo Trolley.
Ergonomics. Ergonomics is important for both guests and guides. For your guides, consider the ease of handling the trolley during the attachment and detachment processes, as these steps are critical for safety, are repeated numerous times a day, and are opportunities to inspire trust or lose trust with the participants. For guests, be aware of the ease of transporting the trolley (attached to them or carried), comfort of riding the zip line with the lanyard or crossbar attachment, and the comfort of the braking experience.
As with all design decisions, there are trade-offs. Weigh and prioritize features, cost, and durability, and choose wisely.
Testing and regulation requirements. The testing requirements for zip line trolleys vary. Be vigilant and educated on the testing certification requirements implemented by your local regulators, certified course inspectors, and insurance company.
Common tests include pull tests, destructive testing, and cycle testing to ensure that the design and manufacturing of the trolley meets safety requirements. Among the many details produced by the tests, the rule of thumb in the U.S. aerial adventure industry is that the trolley assembly must be tested to a minimum breaking strength of 5,000 pounds (22.2kN) at the connection point. The maximum load limit is oftentimes etched on the equipment, just as with carabiners. If a trolley doesn’t have a load rating associated with it, it’s best to not use the equipment.
Other certification stamps may include: CE, for use in life safety applications worldwide; UIAA, for use in climbing and mountaineering; and NFPA, for certification by the National Fire Protection Association. These certifications aren’t normally all required, but it helps to know they exist so that you can ask more informed questions and make confident decisions.
HOW TO CHOOSE
Got all that? Great. Now, here’s the process I use to determine the best zip line trolley for my customers and their sites.
1. Seek out as many options as possible. This normally involves a lot of Google searching. Good resources to find manufacturers include the Adventure Park Insider “Supplier Directory,” ACCT’s Vendor Directory, and IAAPA’s Member Directory.
2. Apply a big filter to narrow the search. That filter tends to be either cable size compatibility or brake system compatibility. Either will cut down the number of choices and are necessary considerations regardless.
3. Filter further by harness and lanyard connection style. You may need or prefer a single attachment point, or a dual connection style with a crossbar, or perhaps an integrated connector style.
4. Consider the nitty-gritty of regulations compliance. This can take some time, but the trolley you choose must meet any state and/or local requirements, so it’s unavoidable. If you haven’t filtered by brake system compatibility yet, this is the time to do so.
5. Final due diligence. At this point, you’ve narrowed it down to a few trolleys that meet your criteria. Time to verify specs and suitability with a few phone calls or emails to suppliers, manufacturers, and other qualified parties. This is the point at which ergonomics, special features, field serviceability, parts availability, and price can become deciding factors.
When choosing a zip line trolley, making an informed decision means paying attention to small and often nuanced details. Keep your priorities straight and your end goal in mind. Remember, in the end, the zip line trolley is a simple machine with a simple job: to keep people safe while they are having fun.
Trolley Manufacturers
Note: trolleys from many of these manufacturers are available from suppliers such as Aerial Adventure Tech, Ropes Park Equipment, American Adventure Park Systems, High Country Hardware, Peak Trading Corp., and many others.
Head Rush Technologies www.headrushtech.com
ISC www.iscwales.com
Kanopeo www.kanopeo.com
Koala Equipment www.koala-equipment.com
Kong USA www.kongusa.com
Petzl www.petzl.com
Robertson Harness www.robertsonharness.com
Skyline Ziplines www.skylineziplines.ca
Xtreem Ziplines www.xtreem.co
ZipFlyer www.zipflyer.com