PRCA Hosts Annual Conference
The Professional Ropes Course Association (PRCA) held its 16th annual conference March 7-10, 2019, at the Holiday Inn Westshore in Tampa, Fla. More than 50 people attended, including aerial adventure operators, volunteers, presenters, and exhibitors. The biggest change for this year was holding the event at a paid venue rather than a volunteer location or campgrounds, according to Steve Gustafson, VP, board of directors for PRCA.
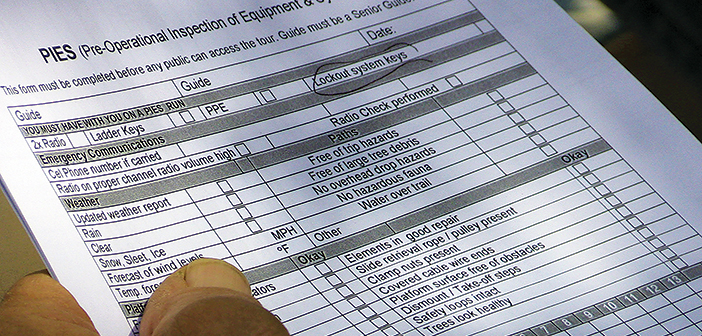
Conference workshops covered a variety of topics, from facilitation and communication to course inspections and lessons learned from a serious accident at a camp. In addition, there was an ASTM F2959 scope meeting (concerning the proposed elimination of the standard’s exclusions for therapeutic, educational, and experiential programs and camps), PRCA consensus body meeting, as well as board and membership meetings.
Attendees were able to engage with a half-dozen exhibitors who were there promoting their products and services, including KONG USA, Kanopeo, Koala, EBL Zip Lines, Hibbs Hallmark Insurance, and CMI. Off-site activities included a boat tour and a visit to nearby Tree Umph! aerial adventure park.
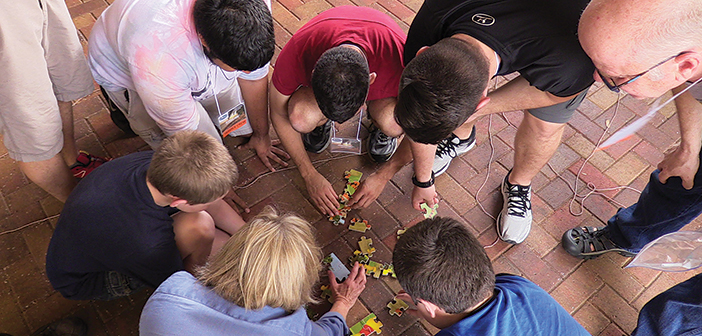
The 17th annual PRCA conference will be held at the same Holiday Inn Westshore, March 5-8, 2020. Discounted rates will be available for early registrants. A call for presenters will go out mid-summer 2019.•
9 Things to Know About OSHA
By Patrick Ferebee, Director of Ecommerce and Product Strategy, Aerial Adventure Tech
You are likely aware of the need for Occupational Safety and Health Administration (OSHA) compliance. But where do you begin? Here are nine things to know first.
If you are an aerial adventure or climbing gym operator, you have likely heard rumblings about the need for OSHA (Occupational Safety and Health Administration) compliance and thought, “Why do I care, and where should I begin?” There is a lot packed into this conversation, and our goal is to begin to shed light on this nuanced topic.
Here are the top 9 things you should know when it comes to OSHA compliance for your operation:
- OSHA Compliance is Law
- OSHA Compliance is the Employer’s Responsibility
- OSHA Isn’t Just Concerned with Work-at-Height
- Start with a Hazard Analysis
- Personal Protective Equipment (PPE) is a Last Resort
- Don’t Forget Rescue Plans for Staff
- Documentation Is Important
- OSHA Inspections Can Be Proactive and Low Consequence
- Educational Opportunities Exist
Now let’s break these down.
1. OSHA Compliance Is Law
Most organizations are aware of this, but do not act accordingly. Your business is probably diligent with documentation and compliance concerning other laws that affect it, such as tax law or labor laws. But for some reason, many adventure-based organizations see OSHA compliance as low priority and give it passing attention. In addition to the obvious ethical obligation to protect your employees from harm, there is serious financial risk to your business if found to be non-compliant with OSHA regulations. The less serious categories of violations have a maximum penalty of just over $13,000 per citation. Willful or repeated violations are capped at $132,598, with even higher fines and criminal conviction possible. Maybe it’s time you bump OSHA compliance up on your priority list?
2. OSHA Compliance Is the Employer’s Responsibility
It’s easy to assume that the professionals you hire to design, install, train, and maintain your facility are paying attention to all of your OSHA compliance needs. While your service provider is expected (and often required by standard) to provide you with products and services that comply with relevant municipal, state, and federal laws, the provider is not the entity ultimately liable for OSHA violations. Your vendors, as qualified professionals, are great resources, and you should tap them for advice and instruction whenever possible. But the documentation, training, and refinement of your employee safety program falls on you, the employer.
3. OSHA Isn’t Just Concerned with Work-at-Height
While fall protection violations are the most cited violations over the past 6 years (note that hazard communication is second in most years), OSHA is generally concerned with the health and safety of workers. OSHA standards cover everything from signage and sanitation to first aid and hazardous substances. So there might be a variety of OSHA standards to consider, such as when, say, an employee is applying chemical weed control on your property. Comb the standards and ensure the proper policies, procedures, documentation, and protective measures are in place for each aspect of your operation.
4. Start with a Hazard Analysis
You might have heard these called by a few names: Job Hazard Analysis (JHA), Risk Assessment, Hazard Assessment and Identification. Hazard analyses are the first critical step in making hazards transparent to employees and implementing the proper controls to protect them. Hazard analyses are even a worthwhile exercise for hazards your participants may encounter.
5. Personal Protective Equipment (PPE) Is a Last Resort
PPE and safe work methods have dominated the conversation around OSHA compliance in both the climbing gym and aerial adventure industry—for good reason, as strides need to be made in that area. But in the hierarchy of controls for hazards, PPE is the last resort. PPE only protects the user wearing it, can never provide 100% protection, and even with specific training always has the potential for user error. Based on your hazard analysis, assess where you can minimize and eliminate risk before deciding what PPE is necessary.
6. Don’t Forget Rescue Plans for Staff
OSHA requires that a rescue plan (or Emergency Action Plan) be in place for employees working-at-height and that they receive practical training on these procedures. Pretty much every operation has a rescue plan in place for their participants (even if it is just to call the fire department). Have you accounted for the rescue of a staff member, though? Work through the worst-case scenarios: an unconscious worker suspended on rope while routesetting; an employee that has taken a fall and deployed their energy absorber; a lead guide on a canopy tour that is unresponsive on a distant platform; or whatever scenarios present themselves at your site.
7. Documentation Is Important
Documentation often comes up as an afterthought, when in reality it should be your first step. A hazard analysis gets things started, but there are other requirements based on your type of business. For example, you will likely be required to identify all necessary PPE for employees, certify that the PPE has been provided to them at no expense, and that employees have received training in how to utilize it. Additional documentation may include Emergency Action Plans, blood-borne pathogen exposure programs, and work-related injury and illness logs.
It is critical to understand what documentation is necessary and the requirements to retain those documents over time. Remember that documentation is evidentiary, so whether required by law or not, it can be used by OSHA for regulatory citations. We recommend reaching out to an OSHA expert who can evaluate your business activities and outline the specific documentation requirements for it.
8. OSHA Inspections Can Be Proactive and Low Consequence
OSHA is not some nagging entity that is just out to fine your business and make life hard. Their mission is to protect the health and safety of workers, and OSHA staff are available to help you find gaps at your site or interpret standards. Very often, you can contact a local inspector and ask him to audit your operation. OSHA inspectors do this free of charge and offer a list of infractions to remedy. Doing this can both familiarize your regional OSHA office with the unique aspects of our industries and allow you time to resolve compliance gaps before an unannounced inspection or employee incident.
9. Educational Opportunities Exist
This world is admittedly hard to navigate, and the push for compliance is fairly nascent in our respective industries, even though compliance has been necessary all along. Resources and formal training do exist, with some info being easier to digest and interpret than others. Here are some places to get started:
Standards and Expanded Resources
OSHA
1926 Standards – Construction
OSHA
1910 Standards – General Industry
OSHA Summary of Fall Protection Standards for Non-Construction
OSHA Pamphlet on Protecting Zip Line Workers
ASTM, ACCT, PRCA, and CWA all approach requirements
for employees in varying degrees, so look for us to unpack that in a later article.
Additionally, we will talk
more about the roles of ANSI standards and testing in later articles.
Books
North American Working at Height Handbook
This
handy field book was developed by leading companies in the work-at-height world
and is definitely the most digestible resource out there. We recommend every location
have this on their bookshelf, and every industry pro own a copy. While is doesn’t
necessarily address every aspect of OSHA compliance, if you work through the recommendations
in this book you’ll be well on your way.
Training
OSHA
Training Requirements and Resources
To
assist with your in house trainings and a quick reference on what standards require
training be given.
OSHA
Outreach Training Program
Receive OSHA certified training with basic and advanced options available.
Learn more about OSHA-compliant PPE at www.aerialadventuretech.com.
1. OSHA Compliance is Law
Most organizations are aware of this, but many do not prioritize accordingly. In addition to the obvious ethical obligation to protect your employees from harm, there is serious financial risk to your business if found to be non-compliant. The less serious categories of violations have a maximum penalty of just over $13,000 per citation. Willful or repeated violations are capped at $132,598, with even higher fines and criminal conviction possible.
2. OSHA Compliance is the Employer’s Responsibility
You might reasonably assume that the professionals you hire are paying attention to all of your OSHA compliance needs. While your vendor is expected (and often required by standard) to provide you with products and services that comply with relevant municipal, state, and federal laws, your vendor is not liable for OSHA violations at your site. Your vendors are great resources, and you should tap them for advice and instruction whenever possible. But the documentation, training, and refinement of an employee safety program falls on the employer.
3. OSHA Isn’t Just Concerned with Work at Height
While fall protection violations are the most-cited violations over the past six years, OSHA is generally concerned with the health and safety of workers. OSHA standards cover everything from signage to sanitation. Comb the standards and ensure the proper policies, procedures, documentation, and protective measures are in place for each aspect of your operation.
4. Start with a Hazard Analysis
You might have heard these called by a few different names: job hazard analysis (JHA), risk assessment, etc. Hazard analyses are the first step in making hazards transparent to employees and implementing the proper controls to protect them.
5. Personal Protective Equipment (PPE) is a Last Resort
PPE and safe work methods have dominated the conversation around OSHA compliance in the aerial adventure industry, and for good reason, as strides need to be made in that area. But in the OSHA hierarchy of controls for hazards, PPE is the last resort. PPE only protects the user wearing it, can never provide 100 percent protection, and always has the potential for user error. Based on your hazard analysis, assess where you can minimize and eliminate risk before deciding what PPE is necessary.
6. Don’t Forget Rescue Plans for Staff
OSHA requires that an Emergency Action Plan be in place for employees, and that they receive practical training on these procedures. Pretty much every operation has a rescue plan in place for its participants. Have you accounted for the rescue of a staff member though? Work through the worst-case scenarios, like an unconscious maintenance worker suspended on rope, and plan and practice for these situations.
7. Documentation is Important
A hazard analysis gets things started, but there are other requirements based on your type of business. For example, you will likely be required to identify all necessary PPE for employees, certify that PPE is available to them at no expense, and that employees have received training in how to utilize it. Additional documentation may include Emergency Action Plans, blood-borne pathogen exposure programs, and work-related injury and illness logs. Remember that documentation is evidentiary, so whether required by law or not, it can be used by OSHA for regulatory citations.
8. OSHA Inspections Can Be Proactive and Low Consequence
OSHA’s staff is available to help you find gaps at your site or interpret standards. Very often, you can contact a local inspector and they will audit your operation and offer a list of infractions to remedy. Doing this can both familiarize your regional OSHA office with the unique aspects of our industry and allow you time to resolve compliance gaps before an unannounced inspection or employee incident.
9. Educational Opportunities Exist
This world is admittedly hard to navigate, and the push for compliance is fairly new in our industry—even though compliance has been required all along. Resources and formal training do exist, so check out the digital version of this article for links to expand your knowledge.•
ACCT Conference 2019
Continued growth in the number of businesses getting into the aerial adventure industry was on full display at the 2019 Association for Challenge Course Technology (ACCT) Annual Conference and Expo, held Feb. 7-10 in Denver, Colo. More than 1,000 people attended the event, which gathers traditional and commercial aerial adventure operators, as well as suppliers and speakers from around the world.

More than 100 different workshop sessions covered every aspect of business and operations. From teambuilding, facilitation, and gamification to finance, marketing, risk management, and more, attendees could learn about the latest trends and best practices.

Read the full wrapup and check out the gallery of photos from the show at www.adventureparkinsider.com.•
Standards and Regulations Advancing on Several Fronts
By Rick Kahl
It’s a busy time for standards and regulations. At press time, several developments were in the works:
• ASTM was balloting new language regarding the scope of the ASTM F2959 standard, once again aiming to eliminate the exclusions for educational, therapeutic, physical fitness, teambuilding, and other “non-commercial” operations.
• ACCT was nearing completion of work on a new edition of the ANSI/ACCT standard.
• PRCA was working to refresh the ANSI/PRCA standard, which is now in its fifth year, and in need of updating.
• Colorado was considering new rules for aerial parks, Utah passed and signed into law an amusement park standard—the state’s first—including aerial adventure parks, and North Carolina was considering two regulatory bills.
• ACCT’s operations accreditation program, which can be seen as a sort of “voluntary standard,” was moving forward and approaching a launch date.
ANSI/ACCT 03-2016 STANDARD
The new edition of the ANSI/ACCT standard, currently nearing adoption, contains some key revisions. Perhaps the biggest: a revamped operations section.
A session at the ACCT Conference in February pointed out that the changes stemmed from the goal of creating an effective standard for commercial parks. The original ANSI/ACCT standard didn’t really address aerial adventure parks; the new edition has an entire section related to them.
The new standard prescribes practices based on the operating system used on the course. It more clearly delineates the requirements for different types of activities, such as aerial trekking, zip lines, facilitated programs, etc. That should make it easier to follow, and to find the relevant info for a particular operation.
For example, the function of monitors is more clearly defined; the standard includes a chart that details the level of monitoring needed for different types of safety equipment (lobster claws, smart belays, etc.).
Some language has been incorporated from OSHA, primarily in sections that apply to employees and PPE.
The new edition also contains small revisions to design, performance, and inspection sections, primarily editing changes to clarify particular points and make the standard easier to understand.
To make the standard less costly to produce, and thus easier for operators to buy, ACCT is removing some ancillary materials from the standard, such as practitioner certification, and publishing these separately.
ACCT expected to submit its BSR9 form to ANSI, seeking ANSI’s approval of the development process, by mid-April. Pending approval, the new edition of the standard could be published soon.
Consensus meetings.ACCT is already working on revisions for the subsequent edition of the standard. ACCT has posted the dates for upcoming consensus meetings, at which members can hear about and comment on proposed changes, on the ACCT website. “We want people to take part, so they understand the process and get involved,” says Scott Andrews, ACCT policy director and secretary for the Consensus Group. “That’s how we get a better standard.”
One task group is working on operating at height, to align the ANSI/ACCT standard with OSHA regulations and bridge gaps between the two. The current ACCT standard omits workers at height; it applies to participants only. On the other hand, OSHA regulations are aimed at the construction industry, and don’t always translate smoothly to the aerial adventure world.
Harnesses are a point of focus. Language currently under consideration will spell out when less than a full harness for staff as well as participants is appropriate, and when something more is required. Certain body types, or circumstances in which participants can be put into difficult situations, may dictate use of more than a seat harness.
ASTM F2959-18
On March 22, ASTM F2959 Evolution Task Group head Jeff Borba initiated a ballot on the revision of ASTM F2959-18 regarding the scope of the standard. Last October, the Evo task group had proposed eliminating the exclusion of many “non-commercial” aerial operations from the F2959 standard. After members of ACCT and PRCA raised objections to some of the language, the F2959 committee agreed to table that proposal for a year.
However, the task group assigned to work on alternative language regarding the exclusion had made little apparent progress. So, following comments received at the ASTM meetings in February, Borba drafted new language intended to reflect those comments and submitted it to ballot. The voting period was to end April 22.
The main change was the addition of a section under “Scope” that reads, “Scope of this practice does not specifically address all human factors, particularly those intrinsic in certain educational curriculum; physical fitness, therapeutic, training and team and confidence building programs; and organized competitive events.”
The new ballot caught many in the aerial adventure world by surprise, since they thought new language would be considered at the ASTM meetings next October. Some were less than pleased by the March ballot.
PRCA president Mike Barker, the industry lead for the scope revision, conducted a working session on the scope language at the PRCA conference in early March. He told Adventure Park Insider that his task group discussed several possible language options, which he planned to describe in his ballot.
Though the balloted language was quite different from what his group was pursuing, Barker suggested the ballot language might be acceptable, if it referenced the ANSI/ACCT and ANSI/PRCA standards for the cited activities.
ACCT was preparing a formal response to the ballot as we went to press.
In an email to voting members, F2959 chairman Jared Krupa said, “To clarify, if this ballot is supported, it will replace the original scope revision document and move forward to publication, and if it is rejected, then the task group will consider both the original and new drafts and decide how to move forward.” The ballot will be taken up at the ASTM F24 meetings in October.
In the meantime, work continues on several other aspects of ASTM F2959-18, including braking, wire rope, geotechnical requirements, updates to the F1193 standard, SARC test, via ferrata testing, and auditing requirements.
Krupa said that input on the scope ballot should be directed to Borba at [email protected]. Questions about other revisions can go to Krupa at [email protected].
Krupa, Barker, and ACCT policy director Scott Andrews all urged interested non-members to join the organization and participate in future activities of the F24 committee and the F2959 task groups. For general questions about ASTM International/F24 and membership contact Katerina Koperna at [email protected].
On a related note, Krupa, Barker, and Andrews all said that work on harmonizing all three standards—ASTM F2959, ANSI/ACCT and ANSI/PRCA—has been progressing. The aim, Andrews said, is to “find and fix the blind spots in each of the three standards,” and tailor them “to suit the industry across the spectrum, from amusement parks to experiential, educational, and therapeutic programs.”
ACCT OPERATION ACCREDITATION
The long-considered ACCT operation accreditation program is coming closer to fruition. While some details remain, not the least of which are cost and how to certify the program’s reviewers, the outlines are becoming clearer.
Accreditation will involve an on-site inspection and a review of operations and training. Much of that revolves around the operations section of the ANSI/ACCT standard. Accreditation will be based on a review of documentation of procedures and training, as well as a review of the operation in action.
At the ACCT Conference, ACCT policy director Scott Andrews emphasized that the inspection is not a simple “pass/fail” test, as an operator would have a limited amount of time to correct deficiencies and still become accredited. But he also emphasized the importance of reviewing the requirements and correcting any deficiencies before initiating the review process, as that can vastly speed the timeline and reduce the potential for headaches.
“I hope this process helps people learn whether what they are doing is acceptable, but also learn what they could do better. The aim is to raise the bar,” he said.
ANSI/PRCA 1.0-.3-2014
This is the five-year anniversary of the ANSI/PRCA standard, and as such, it is due for renewal. A PRCA consensus group is working on that project. PRCA president Mike Barker encourages interested parties, both vendors and operators, to join the effort. Some of that involves simple edit changes, but some sections—such as emergency braking—are more involved. “We want to expand on emergency braking and other areas to reflect and update the standard, to take account of changes and innovations in the industry,” Barker said. The effort will also include harmonizing the ANSI/PRCA standard with ASTM and ANSI/ACCT where possible, he added.
STATE NEWS
Colorado is updating its amusement rides and devices regulations, which specify application of the ASTM F2959-18 standard for aerial adventure courses and zip lines. A stakeholders meeting was scheduled for April 1 (no kidding). The regulations, administered by the Division of Oil and Public Safety in the Department of Labor and Employment, include requirements for daily and annual inspections and recordkeeping for same, and a provision for reporting injuries caused by the malfunction or failure of a ride or device, or by operator or patron error. Proposed effective date is June 15, 2019.
The Utah legislature has passed the Amusement Ride Safety Act, regulating amusement rides and zip lines in the state for the first time. Utah had been one of six states with no regulations for amusement parks. The bill has been in the works since early 2019, and moved swiftly through both houses of the legislature. It arrived on the Governor’s desk for signing into law on March 22.
Among the bill’s provisions, it specifies that ASTM F24 Committee standards will apply (for aerial parks, that means ASTM F2959). It also details annual and daily inspections, insurance requirements, and other activities. The provisions are to take effect in April 2021. The bill gives authority for the regulations to the Utah Department of Transportation. The department also oversees the Utah Passenger Ropeway Safety Committee, which regulates the operation of ski lifts. The amusement park bill was modeled after the lift regulatory system.
The North Carolina House is currently home to two competing bills, neither of which appears close to adoption. One, HR 380, would require daily and annual inspections, injury reporting, and adherence to ACCT, PRCA, ERCA (European Ropes Course Association) or ASTM standards, depending on which is or had been followed during construction. That bill has failed to move beyond the Judiciary Committee. A second bill, HR 395, is much simpler, and specifies adherence to ANSI/ACCT. It was first submitted to Judiciary for consideration on March 21. •