Since its introduction in 2013, improvements have been made for both rider and operator. Last year, a better suspension system and new harness were introduced to create a more comfortable ride. The composition of the brake wheel that makes contact with the track is now more durable, and has better traction than earlier iterations. Finally, the diameter of the pipe (i.e., the track) has grown from three to four inches, allowing for more varied turns, dips, spirals, and drops.
There are currently three Fly-Lines operating in northern Italy, with another being built in Germany. According to Horan, Fly-Line is expected to make its U.S. debut in 2016, with two to three installations planned by year’s end.
ROLLGLIDER
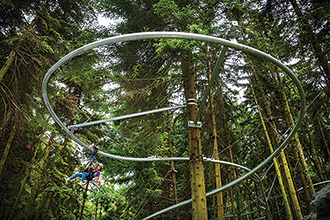
Walltopia’s Rollglider entered the market in 2014 and features three rider positions, including sitting, superman, and tandem.
Headquartered in Bulgaria, Walltopia has been a leading manufacturer of artificial climbing structures since the company was founded in 1998. In 2012, Walltopia diversified into the adventure industry and developed the Rollglider, which came to market in 2014.
With a top speed of about 34 mph, the Rollglider is designed to get the rider’s heart pumping. So are the riding options: sitting, superman, and tandem. Traveling through twists, turns, ups, and downs at high speeds can be jolting on the body, so Walltopia does a computer simulation during the design process to determine how the body will react to the features along the rail. “This way we make sure the ride is safe and enjoyable at every point,” says business development manager Boryana Levterova.
As an indication of how quickly the technology in this activity-which-can-not-be-named is evolving, the Rollglider trolley has gone through seven iterations already. According to Levterova, “With every iteration, we aim to increase and improve the functionality, while minimizing the amount of structure,” she says. “In the last iteration, our R & D team was able to eliminate 40 bolts. The newest iteration is more rigid, easier to assemble, and provides for a smoother ride.”
Walltopia manufactures the 108 mm-diameter rails and pre-assembles the ride at its factory to make sure everything fits properly before shipping to the site. Once on-site, the rails are bolted together with no welding. Installations include start and finish platforms, each up to 10 feet tall, and located relatively close together, so the trolley can easily travel on an automatic return system back to the start. Depending on the size and design of the ride, the Rollglider has a throughput capacity of up to 60 people per hour.
ZIP-COASTER
The newest member of the group, Zip-Flyer’s Zip-Coaster debuted at the 2015 IAAPA expo. It will make its operational debut this June at a park in Mexico, where eight Zip-Coasters are being installed to take riders on speed-controlled tours through the forest and other natural structures.
“The park is built around the concept of stirring your senses,” says Dan Brennan, Zip-Flyer director of business development. “The lines are sweeping gentle slopes that start in the tops of the trees and descend right through the canopy, and ultimately plunge into the earth through natural cave systems—all while flying prone-style.” While these first installations are customized to be less thrill ride and more rolling tour, the Zip-Coaster’s braking system allows it to reach speeds up to 45 mph. “We can customize the ride experience offering a scenic tour or a thrill ride or some of both in the same course,” Brennan says.
Zip-Flyer, having licensed Head Rush’s Eddy Current Magnetic technology, designed the trolley to govern rider speed through a combination of onboard progressive braking and magnetic dampening. This allows the Zip-Coaster to handle high speeds, steep grades, and tight turns in relative comfort.
The rail system is built as a full loop—it includes an uplift system that transfers trolleys back to the launch tower. It can also be built to transfer the rider along with the trolley. That option opens up the opportunity to combine the launch and landing functions in one tower, eliminating infrastructure and saving cost.
Brennan says the modular Zip-Coaster system can be installed just about anywhere, but the company never hangs its rails from trees. “We build steel support towers to control the dynamic forces of the ride and mitigate risk,” he says.
The company has six installations planned in the U.S. over the next 6 to 18 months, ranging from full-on thrill rides to more leisurely speed-controlled tours. The Zip-Coaster has a throughput capacity of up to 90 riders per hour.
THE UNKNOWNS
Costs can range widely, from $250 to $450 per linear foot for these products, including design, trolleys, and other additional equipment and services. Some manufacturers charge on a project basis and not per linear foot because the elements of each installation are so customized. That’s why dialing in the cost can be a challenge, says Paul Cummings of Strategic Adventures. “The pricing we’ve been getting ranges widely, because each one is so customized and requires specific manufacturing and design. It’s not like figuring out the costs to install a zip line that runs from A to B and you string up a line. For these, there is not an off-the-shelf solution.” With more variables in play, costs can vary quite a bit.
Another question to answer: once an operator has made the decision to install one of these new attractions, how does one present the concept to the local jurisdiction in the permitting process? Applicants will likely need to provide an accurate representation of what they are planning to install, and convince the grantees that it’s a low-risk attraction. But that, says Cummings, is not a new battle: “We fought this for a long time with zip lines in figuring out how we accurately portray it and not make it seem like this death-defying thing.”
Those efforts were assisted by zip line manufacturers, who provided clients with videos highlighting the experience. This was tremendously helpful to operators seeking permits, and an effort Cummings thinks might be a good route for zip rail coaster suppliers to emulate as these rides are introduced in the U.S.
Another consideration: since so few of these attractions have been built, who is to say what it takes to build them well? The manufacturers, that’s who. Every company that manufactures a twisted zip rail ride says the components of its products meet or exceed ASTM standards. Engineering stamps are another proof of quality that these companies flex.
What place will gravity-fed twisted aerial rail coaster flying zip rides have in the adventure park world? Time will tell. What is certain is they have arrived in North America, and in the next couple of years, more and more will be operating. Perhaps somebody will even figure out what to call them.