For all the complexity in a zip line operation, guests should never notice any one piece of the system, let alone the condition of the trolley they’re dangling from. This is where rigorous inspection and maintenance come into play, especially for components closest to the user, like your park’s trolleys.
Trolley care is best approached as part of a park’s systematic operating procedure, because trolleys are a key part of a system that needs to function in harmony. And since each system is unique, specific maintenance requirements vary by location.
A variety of factors contribute to what needs to be done at any given operation. Some factors are controllable and predictable, such as trolley component materials and zip line speed, and others aren’t, such as environmental conditions.
“These are incredibly complex systems. It’s like an orchestra: If one instrument is out of tune, everyone else knows it,” says Chris Koske, director of marketing at Head Rush Technologies, which manufactures the LightSpeed series of zip line trolleys.
By implementing a few basic concepts into your park’s maintenance procedures, your team can keep trolleys functioning smoothly and safely, with less downtime and lower expenses.
GENERAL RULES
Each trolley design has its own needs and maintenance requirements, which should be included in the materials provided by the manufacturer. In addition, all trolleys interact with the other components of the zip line, with at least slight variations for every manufacturer, depending in part on the specific construction and features of the device.
But no matter the manufacturer, trolley maintenance follows a few general guidelines for proper upkeep. “There are things that the user can do to maintain trolleys: a drop of oil here or there, warm water and soap is always good. There are lots of things that can be done to keep things operating properly,” says Kenny Brodin, technical sales manager at Kong USA.
One common theme: Trolleys should be kept clear of dirt and grit, especially on gliding components. The trolley should be washed periodically and as needed as Brodin suggests, and a drop or two of machine oil can often help to lubricate gliding components.
Saltwater will significantly shorten the life of these components, so if a trolley comes into contact with salty water, it should be promptly rinsed off and cleaned. Operators should generally avoid using power or jet washers and harsh cleaning products, though, because they can contribute to quicker degradation of the trolley.
At season’s end, each trolley should be inspected, cleaned, and stored in a dry location, away from harsh temperatures and direct sunlight.
For more product-specific considerations, it’s best to rely on the product manual, along with deliberate technician hiring and training, and a meticulous inspection program for your park’s equipment.
TRAINING + INSPECTION = SMOOTH OPERATION
The first critical component of a trolley maintenance program is investment in training staff on the proper inspection and upkeep of the trolley. But the best investment into a park’s safe operation, according to several people interviewed, is hiring a dedicated technician. The ease of finding such a person depends on location, though. According to Eric Cylvick, CEO of Terra Nova, LLC, makers of ZipRider and ZipTour trolleys, a zip line tour that operates in summer at or near a ski area has a likely candidate pool—the ski area’s lift technicians, who have experience maintaining lifesaving equipment in the park’s specific terrain.
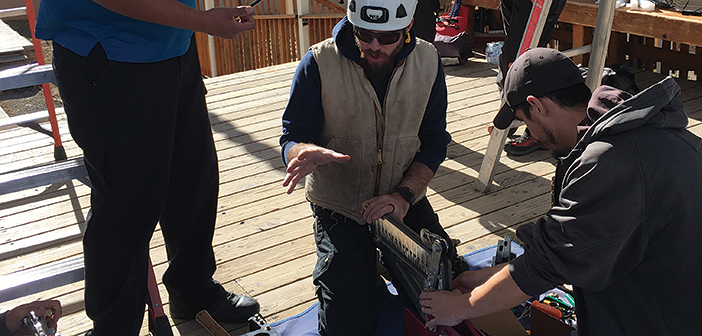
Levi Painter of Terra Nova explains ZipRider trolley maintenance.
More generally, says Cylvick, techs “should have done some form of maintenance in the past: automotive, construction, hydraulic.”
As zip line attractions, particularly in the United States, have trended longer, faster, and higher in recent years, their systems have become more complicated to maintain safely. “With more complexity comes a need for a more highly qualified maintenance person,” says Cylvick.
Even if someone with specific inspection and maintenance experience isn’t readily available, training for the role is. Most manufacturers offer personal protective equipment (PPE) training courses covering the maintenance of their specific products.
For a given manufacturer’s products, the PPE course typically teaches technicians not only the “how” and “what” of equipment maintenance, but the standards behind them. Petzl’s PPE class, for example, begins with the purpose of inspection, including an overview of the organizations that devise standards, such as ACCT, and how they apply to Petzl’s equipment.
From there, technicians learn specific issues to check for in their frequent equipment inspections tailored to that manufacturer’s product. While all PPE courses will include training for maintenance issues specific to the host manufacturer’s products, they also cover general maintenance guidelines that should be applied to the park’s regular equipment inspections.
Enrollment in these training courses isn’t mandated. And since many trolley manufacturers do not have regular contact with operators, says Michel Goulet, Professional Division manager at Petzl America, it’s critical that operators take the initiative to formally train their maintenance staff. “We can only do so much as a manufacturer. Responsibility for inspection and maintenance is really on the owner,” says Goulet. “And that’s why that training course is so important.”
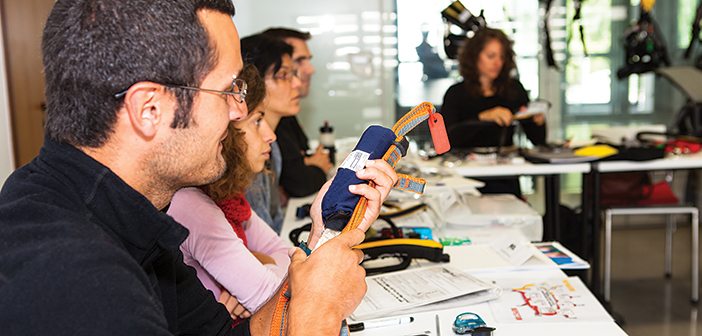
Training, such as Petzl’s PPE competent person course, helps technicians become proficient and knowledgeable.
Photo: Petzl/Lafouch.
LOG EVERYTHING
Once trained, a park’s maintenance team should regularly inspect the trolleys. There are two basic frequencies of inspection for most trolleys: daily and monthly. Together, these inspections provide reassurance about the daily functionality and safety of the product as well as the long-term wear inherent with high-volume daily use.
Daily checks. In a daily check, technicians should focus primarily on proper function. Does the trolley glide smoothly along the cable? Does it interact properly with the braking system? What is the condition of the interface with the braking system? Are any pieces, such as plastic components, missing? Is it visibly worn in such a way that reveals a possible systemic issue with the cable? Beyond function and visual wear, the question asked in a daily inspection, says Cylvick, is, “Can it be put back in service that day?”
If any of these individual inspections reveal abnormal abrasions beyond surface wear, or a change in function, the individual trolley should be removed from service and evaluated for repair or replacement.
Monthly inspections require more time and tools. In these inspections, technicians use tools such as calipers to measure wear points on the trolley, and compare those measurements to what was recorded in previous monthly inspections as well as the original product specs from the manufacturer.
These comparison measurements can expose systemic issues in the operation of that particular trolley, such as how it’s affected by the particular characteristics of the zip line—wind, speed, frequency of use, environmental conditions, and other factors affecting the line.
Annual inspections, in many cases, require that trolleys be sent to the manufacturer for disassembly and testing. Onsite repair of trolleys, for many manufacturers, is limited to replacement of parts, rather than component repair.
Each of these inspections should be documented methodically. This is a critical point: With meticulous documentation of every issue, wear pattern, and daily inspection of each individual trolley and zip line, technicians gain a thorough understanding of the operational requirements of the park’s equipment—an ideal base from which park operators can create their own site-specific operation and maintenance manual.
WRITING YOUR OWN MANUAL
The manufacturer of any trolley sets parameters for safe operation of its equipment based on its own testing and limited feedback from users. But every aerial adventure operation’s equipment is used in an environment where local conditions—wind, temperature, humidity, and workload among them—may dictate modifications to the guidelines. “The purchaser is the only one who can really determine the site-specific things that go on for that particular ride and that particular product,” says Cylvick.
And with well-kept maintenance program logs, you and your technicians can create your park’s unique operating manual. This manual starts with the product specifications and parameters of the park’s equipment, including the trolleys, and merges those specifications with operating logs from your specific site and maintenance program. This custom operating manual serves as a guide for using that specific gear in your site’s specific conditions. Working with your dedicated maintenance staff on this allows for an understanding of the idiosyncrasies of your equipment.
For example, zip line four’s braking system may require replacing the pads more frequently than other lines, due to its steepness. This information only emerges out of consistent record-keeping and analysis of the park’s operation and equipment.
If a trolley is not functioning properly—perhaps a technician notices some unusual condition during a regular inspection or after a unique event, such as a trolley hitting a brake particularly hard or getting stuck in the middle of a line—most manufacturers recommend working with your supplier or the contractor who built the park to determine next steps for repair or replacement.
TALK TO YOUR SUPPLIER
Since trolleys tend to be sealed, enclosed devices, that precludes significant repair onsite. For repairs beyond replacing items such as plastic carabiner covers, there’s usually not a repair your maintenance staff can do that will maintain the trolley’s integrity. Usually only the manufacturer has the equipment necessary to test the trolley to reveal whether a repair, versus a replacement, would keep the device safe for regular use. For example, according to Brodin, the only piece on Kong’s trolleys that is user-serviceable—i.e., replaceable—is the plastic cap covering the holes, which prevents fingers from getting between the wheels and the zip line, that Kong developed per EU regulation.
“Other than that, the bearings are sealed and the gate is riveted to the body [of the trolley],” says Brodin.
Therefore, for operators dealing with malfunctioning or broken trolleys, seeking replacement through the supplier is a safer bet than repair. Upon any inspection, whether daily or monthly, if any doubt exists at all about a trolley’s safe function, it should be immediately retired and the supplier contacted for a replacement, whether through a manufacturer’s warranty or purchasing a new trolley.
It’s also possible that your supplier or the manufacturer will have some insights about the specific maintenance factors for your park’s build. The product’s service team may be able to help isolate any issue that’s causing damage to the trolleys. For example, if inspection reveals that the front of a number of trolleys at your park are damaged and need to be repaired, says Bryan Cox, after sales and service manager at Petzl America, “that typically would look like [the trolley]might be hitting a brake block, so: Have you checked your brake block system anytime recently?”
Trolleys are an essential component of any zip line installation. With regular cleaning, inspection, safe use within product parameters, and the knowledge that comes with meticulous logs by dedicated staff, your park can keep your trolleys working in top condition often for many years—perhaps even beyond the life of the park itself.
TROLLEY SUPPLIERS:
CMI Corporation: www.cmi-gear.com
Head Rush Technologies: www.headrushtech.com
ISC: www.iscwales.com
Koala: www.koala-equipment.com
Kong: www.kongusa.com
-on-the-ropes-: www.on-the-ropes.de
Petzl: www.petzl.com
PMI: www.pmirope.com
Robertson Harness: www.robertsonharness.com
Zip-Flyer: www.zipflyer.com
ZipRider: www.ziprider.com