Equipment failures are rare in our industry, but that still doesn’t prevent patrons at aerial parks, participants in educational programs, staff, and long-standing industry professionals from asking the common question: “How do I know this equipment is safe?”
There are some key steps aerial adventure operators can take to help assuage this anxiety, and some key questions to ask themselves and their vendors regarding safety equipment. Further, there are several actions owners and operators can take, specifically regarding their internal inspection protocols and procedures. The following advice will highlight three key areas to examine—training, frequency, and documentation—and applies to both the individual pieces of gear as well as the overall aerial adventure facilities and systems.
TRAINING
Training on inspection and maintenance of equipment is one of the key steps—but it can be erratic, resulting in staff skipping a formal inspection because something “looks fine.”
To overcome this tendency, ask yourself the following questions:
Are staff properly trained to inspect the equipment they’ll be using? The level of training required for the inspection will vary depending on the type of inspection being performed (more on that later). There are lots of ways to get the appropriate training, ranging from self-directed education using notices, videos, and online materials to brand-specific courses like the Petzl PPE Competent Person course.
What are the goals of the training? When selecting a training or training entity, it’s important to determine what the goal and scope of the training is. For example, the intended outcome of the training may be to train a “competent” person, one who can identify hazards or assess the state of gear; or a “qualified” person, one who may be able to determine how to remedy a damaged piece of gear or component of an aerial park system.
Is the training effective for our staff? For some equipment or componentry, a simple online training or internal training may suffice. For others, it may be impossible to gain inspection competency without handling many of the items themselves and having an interactive experience with the ways they can fail. In this case, the training needs to be in person with a qualified professional.
To determine if a type of training is effective for your staff, consider their level of experience, learning styles, complexity of the item, and possibly also the consequence of the item’s failure. Details matter.
Who is doing it, and what are their qualifications? A training program in equipment use and inspection should be delivered by people who are qualified to do so—which may not simply be an employee who has used it for a long time. Qualification is gained not only through experience, but also specialized training.
So, when selecting a training program or trainer for this purpose, consider the qualifications of the trainer. What are they providing you, and what are their credentials? Additionally, consider their materials. What sort of manuals or notes will they provide? Is there testing? Do staff receive a certificate or acknowledgement of completion?
Be sure to document the trainer’s qualifications and that your staff have gained the correct qualification. Doing so can be an administrative burden—it involves collecting and archiving CVs, portfolios of experience, and maintaining records of employees’ skills and advancement. It’s worth the effort, though: This could be the key to your operation’s ability to prove it is doing the right thing.
A good resource for anyone considering trainings of any sort is the American Society of Safety Professionals standard on Occupational Safety and Health trainings Z490.1 (ANSI/ASSP Z490.1). This standard describes accepted practices on safety training programs, and even has a companion (ANSI/ASSP Z490.2) that provides guidance on e-learning programs of this nature.
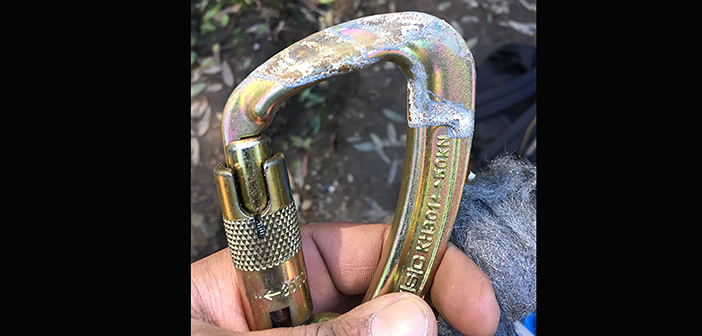
Is this safe? What do you think? Proper training will help determine that.
FREQUENCY
Details matter, and they are often buried in the fine print. Make sure you understand them nonetheless. A few examples:
“Before and after each use, check the state of the stitching and the tape, in particular the state of the edges.”
“This product must be inspected periodically and meticulously, every three months if in frequent use, annually for occasional use.”
“The potential lifetime of this product in use is 10 years.”
All of those are from a “technical notice” or “instructions for use” that come with life safety equipment. Regardless of what it’s called, this document should provide relevant information for the user, including:
• Intended use
• Any specific precautions to note
• Proper care and maintenance
• Inspection criteria
• Product lifetime
• General warnings
• Meanings of markings and declarations of conformity
Though every manufacturer presents these notices a little differently, many require the product to be inspected before every use. Prevailing industry standards and accepted industry practices are aligned on this point.
There are often additional requirements around periodic and annual/professional inspections—typically, that they be conducted in more detail and performed by persons with advanced qualifications.
Some considerations for each of the three types of inspections:
Pre-use inspection: This sort of inspection is usually performed by a “competent” person—one who is trained in assessing and identifying hazards, but may not necessarily be trained in resolving the hazards they identify.
It’s easy for guides and facilitators to overlook sets and components they use daily—routine can result in some lapses in inspection. Rescue equipment inspection can also be overlooked, as it is typically used infrequently. Do not skip pre-use inspections.
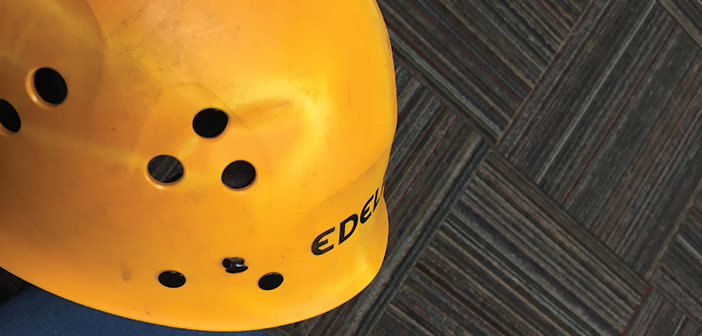
The dent in this helmet is hard to see, and wouldn’t have been found without inspecting every helmet individually.
Periodic inspection: Accepted industry practice and prevailing standards require a qualified inspector to do a more detailed look through the course and its affiliated equipment on a schedule that is generally specified by the manufacturer of the course or elements. Though some operations hire an outside professional to conduct these inspections, they’re often done in-house with a senior qualified team member leading the process—which makes proper training and good documentation even more important.
The main questions to ask when considering this sort of inspection:
Is the inspection schedule reasonable? Most manufacturers specify when and how such an inspection should occur. Organizations may want to increase this frequency based on usage, or conduct inspections before and after surges in usage.
Is this inspector properly trained to evaluate the equipment? As mentioned, being “qualified” takes special training, and may also require considerable experience with a product or system. The manufacturer may offer specialized trainings for items you’re seeking to inspect.
Annual/professional inspection: There are several things to consider when selecting a professional inspector. To start, the authority having jurisdiction (AHJ) and your insurance company may require the inspector to possess certain credentials and levels of insurance.
Additionally, ensure that inspectors are qualified to inspect your particular system; not all zip lines or aerial courses are created equally. Sometimes the manufacturer of the system is the most knowledgeable to inspect your park and its equipment. In some cases, the AHJ may require a third-party inspector. Whomever is selected, it’s always important to consider customer service and report quality in your calculations. An inspection report that is late, hard to decipher, and omits some or all equipment being used can be a problem unto itself. Prior to choosing the inspector, ask to see a sample copy of the report you will receive.
DOCUMENTATION
If it’s not properly documented, it may as well have never happened. Maintaining appropriate documents is critical in an inspection program, especially after all the training, time, and resources needed to properly care for and inspect your course and equipment.
Here’s a partial list of the records you should have:
Staff training: who is trained to do what?
Keep a skill roster for staff indicating what they can do, and when they were last assessed internally and/or externally. It’s especially nice to have syllabi, and records or certificates of completion from any trainings staff have done. A good course operations manual should include different staff roles and affiliated qualifications, required training, and responsibilities.
“Context is just as important as content,” says ACCT operation reviewer Korey Hampton. “If your intention as an operator is to document existing knowledge of your staff, or meet a specific jurisdictional requirement, that may influence or change how you select a training or trainer—you may need it to be documented a certain way.”
Protocols and procedures: Manuals and local procedural documents should also include information on when and how inspections are to be performed. It’s common, and a great idea, to include primary source information, notices, and any other resources from the course manufacturer or component manufacturers. Many equipment manufacturers have great inspection logs and other resources available online; these can also be useful for staff to use and refer to in the field.
Inspection records: Any inspection performed, whether daily, periodic, or professional, should be kept and maintained for as long as required by your manufacturer or local jurisdiction. When in doubt, just keep it in a file.
Equipment inventory and logs: Every operation should have a record of every piece of equipment to track its use as well as when it was inspected, who inspected it, and pass/fail criteria. Digital gear management systems can help ease this task, but will still require considerable time and management. Do it anyway.
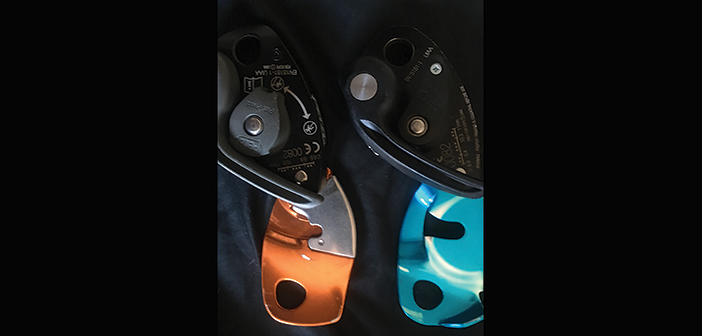
Sometimes comparison is required to determine the level of degradation, e.g., wear on internal plates of grigris.
NEXT STEPS
There’s always room to improve. As you consider what we’ve covered here and contemplate changes to the way you manage your organization, here are two final things to consider:
Are my systems or procedures easy for staff to use and manage? A system, form, or tool that’s difficult to use makes it more likely that staff will skip it or take shortcuts rather than completing the task, especially regarding equipment inspection and inventory management. Make it as easy as possible for staff to complete these things without sacrificing thoroughness. Ensure staff understand the importance of doing it right—and the potential consequences of doing it wrong.
Have I had someone else assess and review this? It’s hard to honestly assess our own operations and procedures—we often get tunnel vision or overlook shortcomings. Consider having someone else take a look to see what you might have missed. This could be as simple as having an industry colleague do an informal peer review, or contracting a vendor to do an assessment of your inspection program, documents, or entire operation. It’ll take some time and maybe some money, but it’s worth doing to ensure that you’re running the safest operation you can.