Getting park guests snugly and safely into harnesses is one of the most critical jobs for guides. A loose strap, an unfastened buckle, a small body in a large harness—if something is amiss in the donning process, all sorts of mayhem and possible tragedy are in the offing. It is often impractical for a guide to do all the fit adjustments for each guest, especially during Covid times, so operators have developed procedures to make do-it-yourself fitting easier for guests. And harness manufacturers have been making the fitting process easier, too.
In recent years, manufacturers have incorporated “anything that makes it easier for people not familiar with harnesses to get [the harness]on and adjust it,” says Kong USA technical sales manager Kenny Brodin. Igor Stomp, owner of harness maker Eyolf, notes that factors besides Covid have been driving the contactless donning trend, including sensitivity toward religiously mandated practices and dress codes and concerns about intersexual touching.
FACILITATED APPROACH
Harnesses that are easier to don are beneficial in several ways, including making it easier for guides to explain the process from a distance. For the inexperienced guest, a harness—particularly the full-body harnesses manufacturers make for aerial adventure park use—can be a puzzling web of straps and tightening hardware. Which way faces forward, and which way backward? Which way up, which way down? Where does the left leg or right arm go? How do you tighten or loosen a strap, and exactly how snugly should the harness fit?
The guide is there, of course, to answer questions like these, and harness makers are taking steps to make the donning process more intuitive and self-accomplishing. Still, Brodin points out that “nothing is going to replace a well-trained guide in making sure nothing gets overlooked.”
Outdoor Ventures and Ropes Park Equipment CEO Bahman Azarm observes that in a typical group scenario, some guests get the donning process right away and some don’t. Those who do can often assist those having a harder time. Instituting a kind of buddy system, based on family units, is one way to accomplish this guest-helping-guest approach.
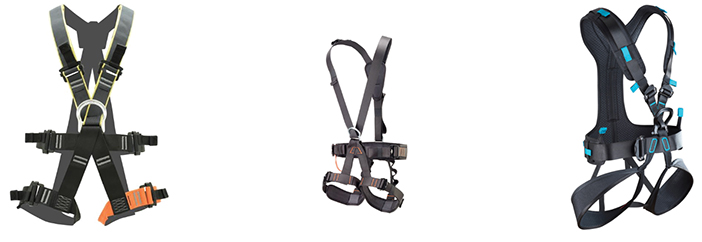
Manufacturers use color in practical ways. Left to right: The Kong Indiana Full II features color-coded leg straps; The Eyolf Cyclone offers customizable colorways; and the Edelrid Radialis comes in a different color for each adult size.
Group facilitation. Challenge Works director of training Rohan Shahani says he has been advocating and teaching no-contact and low-contact interaction between guides and guests since 2016. Shahani adapts the donning process according to the group or client’s needs, but always maintains the core principles of maximizing communication and minimizing physical contact.
“At some tours it’s best to break it down into chunks, one step at a time, with a guide demonstrating each step and the guests following along,” says Shahani. For this, he suggests taking the approach of explain, demonstrate, guide, and enable. “First, tell the guest what the harness is for, how it will feel, and what the finished product will look like. Then demonstrate the process.
“With others, I can demonstrate the whole process and then walk around and provide tips as they don their harnesses,” he says. “Sometimes, someone needs a little extra help, and this is where I’ll ‘guide’ them a bit—entering their ‘bubble’ and showing them how to adjust one buckle or strap. This is usually enough for them to figure out the remainder of the process.”
Shahani says no matter what type of harness an operation uses, it’s important for guides to develop an effective script or language to coach people into them—and practice it regularly.
(For more on the value of facilitation, see “Facilitate the Adventure,” p. 62)
USER FRIENDLY AND EFFICIENT
While the pandemic may have heightened interest in contactless processes and might inform development of new designs in the future, harness manufacturers have long been incorporating features that promote contactless guide-guest interaction.
Primary considerations. Azarm says that two principal considerations have factored preeminently in the design of harnesses specifically for parks (as opposed to harnesses for sport or industrial use): first, efficiency, to speed up operations and improve throughput, and second, user-friendliness, i.e., making harnesses “as idiot-proof as possible—like putting on a jacket.”
Edelrid vice president Blair Williams concurs, saying that Edelrid’s Radialis Pro is designed “to be put on in 20 seconds, unaccompanied, by someone who has never used a harness before.” Deimos owner Tom Clark also stresses simplicity. “It shouldn’t be rocket science,” he says.
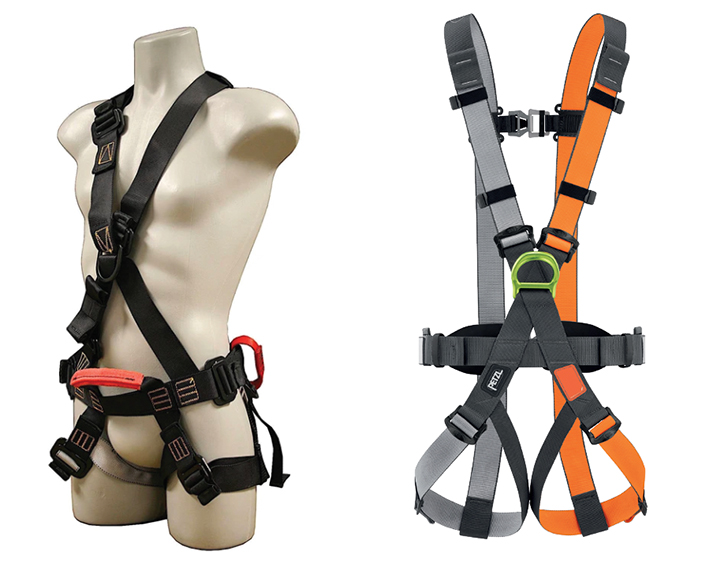
Left: The FrenchCreek Production 4330 avoids any size confusion by making its adult model one-size-fits-all.
Right: Each side of the Petzl SWAN EASYFIT harness is color-coded to make gear-up easier for guests.
In short, the aim is to make a harness so intuitive that a park guest can quickly and easily figure out how to put it on and make initial adjustments, with the guide doing only a final check or adjustment before heading on-course.
COLOR CODING
Perhaps the principal feature harness makers use to simplify donning for customers is color-coded leg straps—one color for the right leg and a different color for the left. Among the many harness models with this design are Edelrid’s Radialis series, the Eyolf Cyclone, Ropes Park Equipment’s EZPZ, the Kong Indiana Full II, the Deimos Eco D-Lite, FrenchCreek Production’s 4330, and Petzl’s new, park-specific Swan models.
Some companies, including Eyolf and FrenchCreek Production, can customize the coloring to a park operator’s preferences. Petzl takes color coding a step further on its Swan models by continuing the use of separate colors for each side up through the shoulder straps.
Starting point. To further obviate which leg goes where, Stomp suggests laying out harnesses on the floor (or ground) so that guests only need to be instructed to step in and pull harnesses up into place. To make that process even easier, painting foot marks on the floor is an additional measure to consider.
Another common color-coding concept is to use different colors for different sizes. This is a design feature used by Eyolf and Edelrid’s Radialis series, among others, which allows customers to choose colors for different sizes. FrenchCreek Production avoids any sizing confusion issues by making its 4330 adult model one-size-fits-all.
In preparing harnesses for guests to step into and pull up over their torsos, laying out harnesses to avoid any confusion about which shoulder strap goes over which shoulder is an obvious measure. On its 4330, FrenchCreek Production makes this process relatively foolproof by featuring only a single strap in the back, which bifurcates just behind the neck. That helps keep the shoulder straps from becoming tangled.
RPE’s EZPZ features a similar design, although the bifurcation is lower on the back, approximately between the shoulder blades.
EASY ADJUSTMENTS
To make harnesses easier for guests to figure out, it can be helpful to reduce the number of adjustment points. RPE’s EZPZ, for example, has just five points of adjustment, as does Eyolf’s Cyclone—two on the legs, two on the waist, and one on the chest.
The key adjustment, says Azarm, is the waist belt. Several harnesses, including RPE’s EZPZ, Petzl’s Swan, and Eyolf’s Cyclone, feature buckles or cinching devices along the sides to allow guests to make initial adjustments easily. Shahani says that a guide can then determine whether a harness is properly fitted through a no-touch visual inspection, or by having a guest demonstrate the snugness of a fit by tugging on straps.
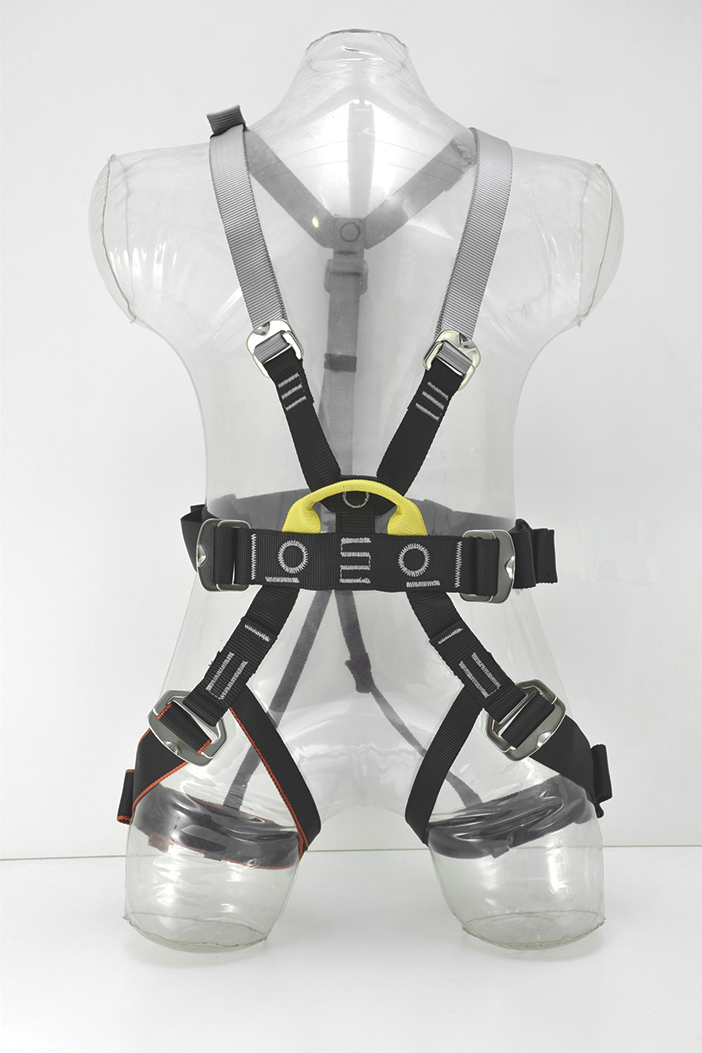
The Ropes Park Equipment EZPZ harness has just five points
of adjustment to simplify the fitting process.
“If your standard process is to tug on a strap to verify its function and fit, ask yourself: ‘Can this be done by the guest and verified by a trained observer?’ In almost every case, it can,” says Shahani.
At least two companies, however—Petzl with its Swan models and FrenchCreek with its 4330—require guides to make final adjustments on the back straps. Petzl accomplishes this in two locations: between the shoulder blades with a lockable buckle, and on the back of the waist with a second buckle. “Up until shutting the clasps on the back, the guest can do [all the adjustments],” says Petzl marketing communications specialist Pat Light. FrenchCreek Production features a single adjustment on the back strap of the 4330.
While these adjustments obviously entail contact between guide and guest, they avoid presumably more offensive (and virus-risky) face-to-face interaction.
SAFETY FIRST
As harness makers continue to design models that are more intuitive for first-time users and operators refine processes that allow guides to make final harness checks with little to no physical interaction with guests, the move toward no-contact or very-low-contact donning should continue to gain momentum.
One bit of advice, however, to park operators from some of our contributors here: check in with your insurance carrier on potential process changes. A park doesn’t want to slip on a liability banana peel if it is deemed that adequate safety precautions were not taken. Efficiency and user-friendliness are important donning considerations, but safety trumps all.
Suppliers
Deimos Zip Harness www.zipharness.com
Edelrid www.edelrid.com
Eyolf www.eyolf.ca
FrenchCreek Production www.frenchcreekproduction.com
Fusion Climb www.fusionclimb.com
Kong USA www.kongusa.com
Liberty Mountain www.libertymountain.com
Misty Mountain www.mistymountain.com
Petzl www.petzl.com
Ropes Park Equipment www.ropesparkequipment.com
SPS Filets www.spsfilets.com