Ski resorts, zoos, amusement parks, cruise ships, and more are increasingly bringing zip lines into their business fold, expanding opportunities for consumers to get in on the thrill. Along with that prevalence has come an increased concern and awareness about safety, especially in regard to braking systems, which have experienced a good deal of evolution over the past decade.
Here we take a look at the status of zip-line braking, and how these systems might move forward with the industry.
Standards and regulations related to zip-line braking are forcing some of the change. Many post-2011 installations, especially commercial operations, require the use of both primary and emergency, or backup, braking systems. Urged on by regulations and operators, who seek effective and high-throughput systems, innovative companies have developed systems that have pushed the industry forward.
Kevin Smith, CEO and founder of Skyline, based in British Columbia, believes the industry’s growth has undoubtedly spurred a great deal of innovation and evolution. “I have been quite impressed with the safety and quality of courses I’ve seen,” he says.
Dylan Burt, general manager for Bonsai Design, agrees that operators, builders, and suppliers have learned a lot over the years. He notes that the higher volume of people on zip lines, and the greater knowledge base that has been developed, have served to educate and inform the industry about where improvements are needed. Even the increasing regulation of the industry has proved beneficial. “I got started in the industry in 2004, and … the innovation and regulation has been great for the end consumer,” he adds.
Active History
Braking began to evolve as zip lines exploded in popularity during the early-to-mid 2000s. This has been especially true for commercial operations, for which passive braking has grown in popularity over active braking. While active braking methods—typically hand braking, in which the rider uses his or her leather-gloved hand to slow down by pressing down on the cable, or some form of guide-activated braking system—are still popular in many applications, the culture and regulations around zip lining have also pushed operators toward passive braking systems that literally take decisions out of the hands of guests.
“When we started, the message to the end user was that this was a recreational activity that you have to participate in. We spent lots of time training participants with the brake, and we were very successful, with very few accidents,” says Burt. “Now, from a braking perspective, [with passive systems]a client is a like a bag of weights that goes down the line. It’s not better or worse, it’s just different.”
Some still see guest or guide involvement as integral to the zip experience. Tommy Cooper, who was a course guide for five years and is now director of operations for Hackwell Innovations, makers of the ZIPKEA brake, saw that guests often liked to hand brake and interact with the guide. But he also gets why active systems are now being “phased out. When a guest is going 25 mph and putting [his or her]hand near the cable, that creates risk,” Cooper says.
Valdo Lallemand, the founder of Aerial Designs, continues to believe in active braking—for guides in particular. The Aerial Braking System (ABS) that he designed eight years ago is a low-cost, active system in which the guide is involved in both the braking and retrieval process. “It’s a simple, robust, affordable braking system,” says Lallemand.
He questions whether automated systems are inherently safer. “Automatic does not necessarily mean safer, it means more automatic. If the operator doesn’t do his job with an automatic system, serious accidents can still result,” he adds.
“I believe it’s important to have someone involved, and I have a number of clients that like and prefer that involvement,” Lallemand notes. He cites an incident at a park with passive primary and backup systems. A guide needed to do a retrieval, and for convenience locked the system to the railing—and then forgot to unlock and reset the brake. “With a fully automated system, the guide can become detached and stop paying attention,” Lallemand says. “If the staff are actively involved in braking, it keeps them sharper.”
A modern spin on active braking is the dynamically controlled trolley brake designed by Terra Nova for its ZipTour systems. The ZipTour trolley has a rider-activated braking system: riders pull down on the handle to release the brake, and let up on the handle to slow down. The interactive nature “creates a much higher repeat ridership,” says Eric Cylvick, founder and CEO of Terra Nova. And, since ZipTours are typically designed as dual, parallel lines, “Our ZipTour trolley makes the experience a lot like skiing, where you can share the experience with the person riding next to you,” says Cylvick.
The Passive Approach
Other companies believe their passive designs reflect the progression of the industry. “In the last 10-12 years, zip lines have really taken off. The demand was outrunning the current technology in the zip-line braking world, and this created the need for our brakes,” says Luke Winkler, a product manager for Head Rush Technologies. Head Rush manufactures zipSTOP brakes, which utilize eddy current magnetic braking, and have become widespread in the industry today.
Mark Reich, senior product development engineer for Head Rush, understands that while some guests prefer to be a part of the experience, the risk from use of hand brakes is real. “There is the human element with hand brakes, the orientation of the rider comes into play, as well as other safety concerns,” he says.
Passive systems function even when a rider is incapacitated, Reich points out. He cites an incident in which a guide was incapacitated by a lightning strike while on a line, but was not injured upon arrival at the landing platform due to the automated brake. Reich acknowledges that this was an incredibly rare occurrence, but says it demonstrates the value of an automated system.
ZipFlyer also employs eddy current technology in its passive braking system. “This gives us the ability to utilize a one-size-fits-all trolley, which accommodates riders 60 to 300 pounds,” says business development and marketing manager Elijah McHenry. “Non-friction braking allows for increased lifespan of trolleys, and eliminates the issue of worn-out brake pads that occurs when using friction braking.” The company’s ZF Track terminal brake also communicates with the launch tower once the brakes have been reset for the next rider.
In addition, the company’s trolleys incorporate speed restriction technology, which “allows our braking systems to operate efficiently and effectively,” McHenry adds.
Another manufacturer, Zip-Rush, advocates that every site be evaluated for the proper braking system, as “zip line brake design depends on many factors: expected landing speed, available braking and buffer zone lengths, type of trolley, and budget.” For that reason, Zip-Rush provides a range of brake options, including magnetic, progressive, spring brakes, and impact blocks.
Going on Spring Brake
Spring brakes—a series of springs and spacers installed on the end of the line to stop the rider—are relatively common, both as primary and backup brakes. The coils compress upon impact, slowing the rider. A potential downside is that riders rebound from the impact, and this might require operators to spend time on retrieval, and therefore lower throughput. While this might make spring brakes impractical for many primary brake installations, they can be “great when used as emergency arrest devices,” as Head Rush has written.
Manufacturer Zip-Rush sees a versatile use for spring brakes. It originally used a spring brake as an alternative to a rubber stopper, but came to learn that spring brakes have a wider range of applications. Zip-Rush now states that spring brakes are “the perfect alternative to most high-speed zip line landings,” and lists this brake choice as one of several in its product lineup.
Terra Nova has its own spring brake system, the Graduated Spring Stack, which it designed and patented in 2001. While Cylvick acknowledges the price can appear high at first, he adds that when factoring elements such as low maintenance costs and no need for a secondary cable to support a brake block, “it becomes obvious that it is a safer and less expensive option, even in the short term.”
Primary and Secondary
Requirements for backup, or emergency, brakes constitute a key portion of zip-line standards and regulations. Without engaging in a thorough discussion of the regulations within each jurisdiction in North America, or detailing the exact differences between ACCT, ASTM, and PRCA standards (the ASTM standard is currently undergoing a revision), it’s fair to say that emergency brakes are required in many commercial operations. These backup brakes are typically required to be fail-safe or involve redundancy that makes them effectively fail-safe—redundant systems are highly unlikely to fail at the same time.
As a practical matter, a main issue is the amount of room available on the landing platform and in the landing zone to install and operate a backup brake. Cooper saw this firsthand when evaluating courses for potential retrofitting with ZIPKEA installations. “Courses are sometimes built without room for one, so they need something small, and that can be difficult,” he says. Additionally, depending on the type of backup brake used, if it is not self-resetting, guides may need to reset two different brakes for each rider. And that can affect throughput, Cooper points out.
In early 2017, Head Rush published a white paper highlighting its policy that requires any system using zipSTOP primary brakes to meet the appropriate standard for emergency brakes, or “emergency arrest devices,” in Head Rush terminology. Head Rush interpreted both the ASTM and ACCT standards to mean that they require a passive and engineerable emergency braking system, and noted that its zipSTOP usage agreement requires such a system. This had a significant impact on the industry. Some operators have been able to meet this requirement easily, but for others it required costly renovations.
For its part, Head Rush argues that its white paper only reinforced existing standards. “Those requirements always existed. There was always language about backup brakes, but some of that was falling off the radar, and it needed to be front and center,” notes Reich of Head Rush.
Now, a year and a half later, Head Rush views its firm stand on emergency brakes as mostly successful. “Initially, a few people were not happy about it, but by and large they have come around,” Reich says. “Most of the time—though not 100 percent of the time—there was a way to figure it out [to get an appropriate backup brake installed].”
Head Rush recommends use of a second zipSTOP or zipSTOP IR as a backup for a primary zipSTOP brake. The aforementioned ZIPKEA is another option.
Another type of backup brake is the Emergency Arrest Device (EAD) designed by Bonsai Designs, which takes up little space and avoids the need for a long deck that a spring brake can necessitate. For primary brake applications, this system can facilitate easy retrieval of participants who come up short of the landing area.
Lallemand reminds that all these options are relatively expensive, compared to the use of a self-retracting lanyard (SRL) and shock packs. “The SRL and shock pack must be engineered for the specific installation,” he cautions.
He also points out that braking systems don’t necessarily have to be based on a primary/secondary model. His preferred system involves three levels of braking: it starts with a zipSTOP, then utilizes his ABS system (which serves for both braking and, when needed, retrievals), and a third emergency brake system consisting of an SRL and shock packs. Such a system is not applicable to every zip line, he acknowledges, but he encourages operators to think beyond a simple two-part model.
The Future
Over the past 30 years or so, zip line braking has evolved from sliding your leather-gloved hand on a cable strung between two trees to utilizing rotating electromagnetic braking technology on a 3,000-foot vertical drop zip line at a 42-degree angle over a roaring ocean. But industry visionaries are looking forward to changes yet to come.
“The most challenging part is braking and maintaining the brakes. Everyone in the industry would like to have more alternatives,” says Smith of Skyline. “People ask me all the time at tradeshows, ‘When are we going to see something new?’”
Perhaps that something will include zip lines that are curved, not simply straight-line descents. Smith is excited about the recent SkySurfer attraction that opened in August in Missouri, which lets the rider stand on a surfboard and go around corners, brake on the line, and even go uphill. This “zip line” utilizes electric motors, onboard batteries, and computer systems to control the speed of the rider on the line, and regenerative motor braking to slow the rider.
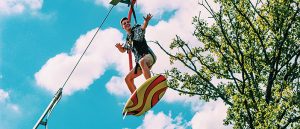
Skyline’s new SkySurfer, which opened in August, allows for cornering, braking and even going uphill.
Speeds may also increase as some parks aim for “fastest” status. To that end, Head Rush is adding its third piece of equipment to the zipSTOP lineup this fall, the zipSTOP SPEED, which is said to be designed for arrivals at up to 45 mph.
Or perhaps the breakthrough will be speed control. ZipFlyer recently patented—and produced—what McHenry calls “an exciting new piece of technology that is about to revolutionize the industry as we know it. The key to this system is called the braking fin. This allows us to restrict the speed of riders on both zip lines and ZipCoasters … to give them a consistent riding experience.”
How will these and other future innovations impact the industry? Time will tell. “Difficult to see. Always in motion is the future,” as a sage once said.