There was a rumbling heard across the industry in the wake of the Hubbell safety advisory last spring that “the days of the wild west are over.” Originally released in March of 2021, the advisory directed park builders and operators to stop installing Hubbell’s deadends and remove them immediately. A subsequent re-release in April 2021 added prohibitions on suspension clamps and pole bands. All that set off a rush to determine how many of these devices were in use, and how best to replace them in an orderly and timely manner.
The eventual responses to Hubbell varied from immediate replacement to, more commonly, a six-month replacement period. A few suppliers, whose own testing showed the components were suitable for the tasks, scheduled a longer replacement cycle.
More broadly, the advisory implied that the industry needed to become more organized, more sophisticated, and perhaps more standardized in the way we run our businesses and the way we build. Hence the declarations that the “wild west” was over.
Just what does that mean, though? What sort of steps does the industry have to take? What are the implications for construction, training, maintenance, and operations?
To explore all this, Adventure Park Insider convened two group calls via Zoom in late summer. In addition to co-authoring this article, Experiential Systems Inc. CEO Keith Jacobs participated in both calls, and also helped to assemble the other participants, who spanned a range from operators and builders to inspectors, consultants, and standards-writers, all hailing from across North America.
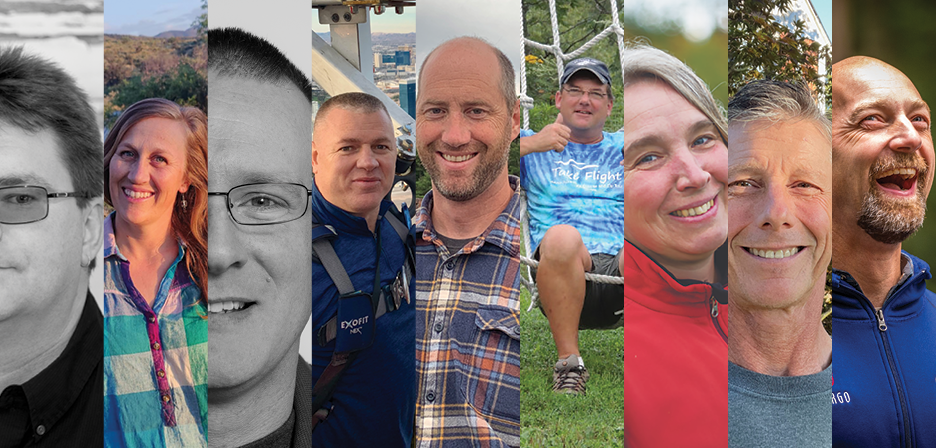
The panelists who participated in our discussions (left to right): Keith Jacobs, CEO, Experiential Systems Inc.; Emily Goff, Owner, Arizona Zipline Adventures; Paul Cummings, President, Strategic Adventures; Jeff Borba, Owner, Precisioneering; Dave Humphrys, President, Elevation Aerial; Charlie Williams, CEO, WingSpeed / Take Flight Adventure Park; Kathy Haras, Vice President,
AdventureWorks; Rich Klajnscek, Owner, Sea Fox Consulting; Erik Marter, CEO, Synergo.
DIFFERENT PERSPECTIVE
According to Rich Klajnscek, owner of Sea Fox consulting and chair of the Association for Challenge Course Technology (ACCT) design, performance, and inspections standards committee, the challenge course and aerial adventure industry isn’t really, nor has it been, the wild wild west, but could best be described “as a collection of industries” ranging from traditional experiential education programs to newer recreational adventure parks.
“Challenge courses were kind of the same for a very long time and were simply being refined by manufacturers and operators,” said Klajnscek. When commercial operations like zip lines, and then later aerial adventure parks, showed up, “suddenly, the accelerator was hit. People and companies were developing products at a speed that we hadn’t seen before. Collectively, the industry wasn’t ready for it—from a standards perspective, and from an equipment perspective.
“So, it’s less of wild west and just more of playing catch up with what other industries had already been doing, as in the amusement device world,” he said.
AdventureWorks Associates vice president Kathy Haras notes that “conventional ropes courses and zip line canopy tours—and later, aerial adventure parks—are really grounded in opposite or different parts of a perspective. When you consider that a good portion of the equipment selected, and practices used in aerial adventure has come from traditional rock climbing—well, if you’re still engaged in those activities on a regular basis, it’s a little hard to call those things the wild west,” Haras said. The equipment and practices are still standard and accepted.
But compared to “a much more amusement-ride oriented environment,” like commercial zip tours and aerial adventure parks, “where things have been engineered, and you’re not just slinging a rope around a rock or over a tree, it’s hard to bring those branches together, because they’re not often rooted in the same perspective,” she said.
Jacobs likened this industry to one that’s still in its adolescence. “We’re no longer a crawling child, but are in our teens. We’re kind of mature. We think we know better in some respects, but we still have lots to learn as we emerge into adulthood,” he said.
WHAT THE WILD WEST LOOKS LIKE
As Hubbell revealed, one aspect of the wild west is using components or materials that are outdated, unapproved, or fail to meet current standards. And that remains a habit, even post-Hubbell.
“I have worked on courses where the guides just pushed up the cable as a brake and caught the guests as they came,” said Emily Goth, owner/operator of Arizona Zipline Adventures. “Truth be told, that felt very safe to me at the time. But most places have upped their acknowledgement of what is going to create the best guest experience and how they can make it as safe as possible.”
Not every operator has done that, though, which contributes to the sense that the wild west still lives on.
Shoestring budgets. “One of the biggest problems we see in this industry is people don’t have any working capital,” said Strategic Adventures president Paul Cummings. “So they sink every penny they have into getting this thing built. … [then]they decide that they can’t afford the inspection, or can’t afford to replace the pieces that they need to. That’s the biggest trouble, really, the lack of capitalization for these new projects.” Aerial adventure parks and zip lines almost always cost $1 million or more.
Something similar occurs on the traditional side of the industry with a lack of long-term planning and upkeep. “It’s often really easy for social organizations or charities to initially pull a grant to get the course going, and that includes equipment and training,” said Haras. “But then they get 5, 10, 20 years in, and the upkeep hasn’t happened, the staff retention hasn’t happened, the training hasn’t happened. So, it’s almost the same problem as with the financing.”
In some cases, consciously trying to cut construction costs results in a wild west situation. “There are manufacturers and vendors and people who figure out how to build stuff less expensively—without the arborist report, without civil or structural engineering, without the permit,” said Jacobs. “In these instances, I would argue the wild west is very much still alive, if that’s my definition of it.”
In other cases, though, it may just be a lack of awareness or industry knowledge. “Part of this, too, is that people who built this maybe 20, 25 years ago, they just haven’t kept up with standards,” said Cummings. “They haven’t seen a need to since they built it. Or, like Kathy said, it has probably changed hands so that historical knowledge wasn’t passed down, the need for training, inspections, all those things.
“It’s not that they don’t care. They just don’t know that this stuff is there.”
A role for regulation. How to overcome that lack of knowledge? “I think it’s regulation,” said Jacobs. “When Michigan regulated, we got calls from 30 camps that had never had a challenge course inspector [on site].” Now that the state was asking for a third-party inspection report and if camps follow certain standards for their challenge courses, camp operators had to start complying.
The benefits of increased regulation can only be realized if authorities hold up their end, though. “One place where we do have a wild west problem is where we don’t have enforcement, and where the regulator is engaged in the wrong enforcement,” said Haras.
A downside of grandfathering. “The concept of grandfathering or of service-proven is sometimes a plus for many organizations,” said Jacobs. “It helps them to maintain a simple system that doesn’t really need to be complicated with new technology or processes.”
But sometimes being grandfathered is used as a crutch by operators to keep a system the same because the ACCT standards or ASTM don’t require a change, said Jacobs. “Then it’s me the vendor saying, ‘Yeah, but we’re uncomfortable with this system and it’s not what we’re willing to accept at this point, knowing what we know about the reliability of up-to-date systems.”
So: do grandfather clauses and service-provens keep us in the wild west? What could or should we do, if anything, from the standard-setting world, to help eliminate some of those things that maybe are still wild west leftovers?
Separating good from bad. “It’s about identifying what those items are,” said Haras. “Certainly, a gravity brake zip line is by no means new technology. But if it is rigged correctly, is operated correctly, and has been well-maintained, you don’t need to change it. That’s different from saying, ‘Hey, we’ve upgraded a standard because we discovered this safety factor’s not adequate, or this material isn’t behaving the way we thought it was, so you need to change that old part.’”
People are going to find workarounds or just not keep in compliance, said Cummings. But that could change, he noted, “once the insurers and regulators start to enforce compliance. If you can’t get insured, that’s going to force an evolution from where we’re at now.”
Goff sees some truth in that. “We wouldn’t have been able to open or get insurance if we didn’t get ACCT inspected,” she said. “I’m always scratching my head as to how people are running businesses without meeting these standards and without getting these stamps of approval.”
THE RESPONSE FROM BUILDERS
Builders we spoke with weren’t surprised by the deadend ban, but were surprised by the inclusion of suspension clamps.
For Jacobs, his first reaction to the Hubbell advisory was, “Is this really still an issue for companies? Are people still using automatic deadends?” Most builders had abandoned them years ago, when use of deadends first came into question. (See our earlier online report, “Hubbell Warns Against Use of Its Deadends, Clamps, and Bands,” for more, at adventureparkinsider.com.)
But the suspension clamps have been used by several builders, including Experiential Systems. “Upon receiving that second letter, our first phone calls were to our engineers” who had drawn the suspension clamps into plans, said Jacobs. “They both suggested we immediately look at alternatives because the manufacturer said to stop using them. Basically suggesting that we create a reasonable remediation plan and a timeline that’s appropriate.” Experiential Systems’ insurance agent and legal counsel echoed those sentiments.
So, the company engineered two replacements for the suspension clamp, and had them tested. “We worked with another vendor to test automatic deadends, too, so we had that data to support their continued use on courses we were inspecting until they could be replaced,” he said.
To continue his earlier metaphor, “In the end, this drove some extra maturing, from teenager to young adult,” said Jacobs, who has since started to consider what other commodities may need to be removed from designs and replaced with proprietary solutions.
The utility connection. Dave Humphrys, president of Ontario-based Elevation Aerial, said the Hubbell advisory led his company to examine the components it uses, too, and realized many of them are from the utility industry.
“But at the same time, much of what we do shares a lot of similarities to the utility industry,” said Humphrys. “They string wire rope and they string it under some pretty high tensions at times. So, some of their hardware is very suited for us, and I’m not convinced that our industry is big enough yet to go out and develop a lot of those unique products.”
He pointed out that our industry needs to develop some products, like zip line braking systems, that are unique and serve an industry-specific purpose. “But the utility industry develops hardware that is really generic, like bolts and clamps that come with a strength rating on it that we can then engineer into a system.
“The Hubbell suspension clamp statement surprised me, as it’s really just a component in a system,” Humphrys continued. “And the suspension clamp comes with a rating on it, and is typically utilized in a manner with loads similar to how it was intended.”
Synergo CEO Erik Marter agreed with that. “When we start looking at the products that we use a lot—like copper oval sleeves, for example—those are designed to put an eye in a cable that’s rated for so much, not for any specific use,” said Marter. “Same with the ground anchor. … If our industry says we need to start creating all of our own things and we invent our own cable clamps, etc., that just seems silly to me.”
Use of off-the-shelf components. “This issue has been around for a very long time on all different types of rides,” said Jeff Borba, owner of engineering firm Precisioneering and an active member of the ASTM Committee F24 on Amusement Rides and Devices. “Whenever I see a component that is off the shelf, the first thing I ask to see is the cut sheet to make sure that the designer or the engineer is using it within the limitations set by the manufacturer.
“For example, I recently came across a mechanical clutch that said it was not for use in life safety devices, and it was being used for one. If you’re going to select something off the shelf, which we all do—and we should do—we have to use it within the manufacturer’s requirements for that part,” said Borba.
Documenting successes. To bolster the industry’s position with component manufacturers, “It would be prudent to focus on how successful we are in using some of these materials that are from other industries,” said WingSpeed CEO Charlie Williams. “We should describe how these products have been so successful for us over the years, and that we’ve got documentation on that, records on how we’re using this material within the scope of how it was designed, and in terms of its breaking strengths, so that we should be able to continue to use it.”
Commodities vs. specialized components. “There’s a difference between common commodities used the way they’re intended—like using screws, and bolts as fasteners—and more specialized products,” said Jacobs.
“During our reaction to the Hubbell letter, we looked at other utility-line products we use, and we started to identify and file our paper trail regarding our communications with the manufacturers and engineers about the use of those products,” said Jacobs.
Jacobs said his company uses the phrase “the hot three” to refer to the three things they think are most likely to be pulled just like the Hubbell product was, and engineer a proprietary replacement that will be installed moving forward. “That way,” he added, “a manufacturer of a part from a third-party industry, like utilities, can’t come in later and say it wasn’t designed or manufactured for life support systems.
“We recommend that exercise to others: Select and prioritize the three components that you think are the biggest risks and how to document their use, or how to eliminate those if you can’t properly document their use.”
“The Hubbell advisory created a need to discuss this larger issue of components,” said Klajnscek. “There are so many products used all over the place—like poles that were not designed to hold people up, or wire rope—and we may not be able to chase down every manufacturer of generic commodity products that have known strengths, and are proven to work. They’ve been used safely for decades. I don’t believe our industry is ready, or has the budget, to develop all our own components yet.”
It all starts with having a process. “It’s important to create a process,” said Marter. “And then step two is follow the process. And step three is documenting the process that you followed. Everybody has a problem when they start cutting the corners or they forget one piece or they didn’t document one part.
“The piece that everybody can improve on now is making sure your process is working, and that you’re following your process,” Marter concluded.
Part 2 of this series will appear in the Winter 2022 issue. Only subscribers can read it. Subscribe here.