As many of the commercial zip line tours and adventure parks in the U.S. and Canada have wrapped up their seasons, it’s a perfect time to schedule your third-party inspector’s annual spring visit—and use the time between now and then to prepare for it. Thorough preparation and planning will help to avoid the common errors that inspectors like me encounter, all of which can add time, cost, hassle, or worse.
As a third-party inspector for the last 27 years, I’ve seen these common errors at all sorts of different operations. I’ve highlighted a few of the errors here to help you avoid making them and, ultimately, increase the quality of your programs, safety of your courses, and speed and efficiency of your third-party inspections.
Course Maintenance
Let’s start with the obvious: Do your maintenance prior to the inspection. Read your previous reports, identify the work that needs to get done, and do it. If your inspectors noted that an element needed to be fixed in the next six months, and that was a year ago—get the work done prior to the visit.
Trim your trees. If you have tree branches in your zip line corridor, get them out. If your inspector is zipping down your lines hitting branches, etc., he or she will most likely fail the element. Once an element fails inspection, work will need to be done to bring the element in line with standards. It then must be reinspected—at additional cost—to get a clean bill of health. This is an expensive and unnecessary hassle for all involved.
Keep logs. As inspectors, we want to see your maintenance logs so we can cross reference them with previous inspections and what we are noticing on-site. Maintenance logs help us all understand the history of the course and the small changes made over time to repair aspects of the course and elements. Without a maintenance log, your inspector may not be able to identify course areas that have required consistent attention over time, preventing the inspector from offering suitable recommendations to curb unnecessary wear and repeated maintenance.
Additionally, your log should make note of who performed what maintenance and when. Knowing who performed prior maintenance and the timeframe of completion helps your inspector identify wear cycles, as well as to whom they should direct questions about unusual repairs or suggestions for future repairs.
Access. Inspectors are talented at getting themselves into difficult-to-reach places. That does not mean they should have to! During inspection, your course should be accessible in the same way staff access it for daily use, periodic in-house inspections, and emergency procedures. If you use ladders or cable grabs for access, then have them available. If you need to belay staff to get to the upper parts of the course, then let your inspector know prior to showing up so he or she can plan accordingly.
If an inspector doesn’t have adequate access to a given element, you run the risk of that element not being inspected and therefore not approved for use unless the inspector returns at additional cost to assess the element later. Likewise, your inspector will assess the gear you use to access your course— like ladders or cable grabs—as part of the inspection, so it is doubly necessary to have that equipment available.
What’s This?
I often have questions while inspecting a new site. How do you use this? What gear do you use on this element? What kind of rescues do you do on this element? The answers to these questions help inspectors understand the course. Having a competent and knowledgeable staff person there to answer questions will make for a better inspection. Without an appropriate staff person to consult with, the inspector is left making assumptions that may or may not be true about the site, including:
• Primary age groups served: This affects the type of gear recommended for your site, fall distances given, course gear and design, etc.
• Course usage: Knowing your throughput helps an inspector get a better picture of gear retirement criteria and equipment service life for your course.
• Element location: Many sites have individual elements tucked into the woods. If the inspector can’t locate the element, it will not get inspected.
Where is the whale watch? Your inspector needs to see the course—all of the course. It is a waste of time and money, and a potential liability risk, for elements to be unintentionally (or deliberately) hidden from your inspector. In addition to a knowledgeable staff person who can walk your inspector around the site, a map of your course is helpful. The walkthrough is also a great time to ask your inspector questions as well as share any concerns about the course you may have.
Reports, products, procedures. As part of an annual inspection, we also audit a site’s documentation. Have available for your inspector a clean copy of your:
• policies and procedures manual
• owner’s manual
• emergency action plan
• maintenance records
• previous annual reports
• daily pre-use inspections
• periodic inspection reports
• incident and accident forms
• annual in-house review of safety procedures
• annual in-house review of incidents and accidents
Bonus points for ensuring staff are filling these out completely and correctly.
Other reports that should be available to your inspector:
• operational reviews
• arborist reports
• training documentation
• pole inspections
Having these documents and reports available for review saves your inspector time in searching for them and helps paint a more holistic picture of your operation. While failure to produce this documentation won’t result in a complete inspection failure, the documentation portion of the inspection would be marked as “needing improvement.”
Gear
If your gear has been put away for winter and is not out for the inspection, it creates a challenge for all. Locating gear that has been scattered across the site takes up valuable time during the inspection. Furthermore, gear that cannot be located—and therefore cannot be inspected—may be found once the inspector has left and put back into circulation without being properly assessed, creating easily avoidable risks and liabilities for your site. Make sure your gear is clean, organized, and set out in the gear-up area used during normal operations before the inspector is on-site.
Know your gear. You should know what gear is used where, and how. Knowing what gear belongs to which elements can provide valuable clues for your inspector as to whether there are course changes that can be made to alleviate undue wear on gear. For instance, if your inspector notices a particular wear point on a rope and knows that rope is used for a given element, your inspector can then look at the element to see if there are friction or rubbing points that should be mitigated to prolong the life of your rope. Failure to provide this information can limit your inspector’s ability to make informed and concise recommendations for your equipment and its application on the course.
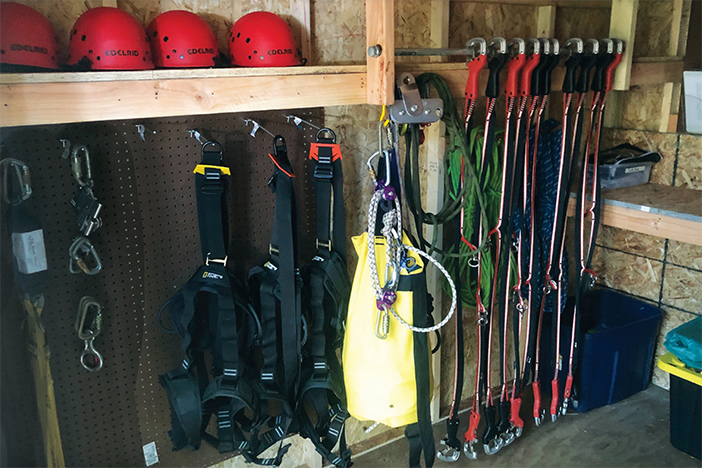
A well-organized gear room with all the necessary items easily accessible—including an up-to-date gear log—will save your inspector time and reduce avoidable risks.
Track your gear. Gear should also be logged into service when it is purchased. This means making note of the type of gear, manufacturer, date purchased, when it was put into service, its retirement criteria, ongoing inspections, maintenance, etc. That documentation allows your inspector to more accurately assess whether a piece of gear needs to be retired or not, as well as whether any annual recertifications are past due. Often, due to normal wear and tear, the labels and/or serial numbers of individual pieces of gear may become lost or unreadable over time. Gear should be easily identifiable and aligned with the logbooks. Sites that don’t have adequate equipment tracking systems, and also experience high staff turnover, run the risk of gear being used for inappropriate, potentially dangerous, applications. For instance, often the “retrieval” cord on a giant swing is of a lesser diameter than the belaying rope. An inexperienced new hire walking into a shed full of ropes that have not been clearly marked may mistake this “retrieval” cord for a life supporting rope.
Next Steps for You and Your Course
Do these things now before your annual inspection:
• Look at last year’s reports and tend to the issues noted by your inspector.
• Go through your manuals and make sure they are a correct and accurate representation of how you operate your course.
• Ensure staff are filling out daily preuse inspections, maintenance logs, incident forms.
• Chat with your inspector NOW to set up next year’s inspection.
Your inspector is one of your best resources—if he or she isn’t, then you may want to consider a new inspector. While I’ve shared some common errors here, it’s worth connecting with your inspector to see what you can do to help them in the inspection process.
TYPES OF INSPECTION
There are many types of inspections that serve different purposes. Below are the three inspections currently required by ACCT standards—of which the third-party annual is a critical component—as well as their relevance and purpose.
Acceptance Inspections
The acceptance inspection, often done by a third party, is part of the commissioning process for a new course, new elements, or major changes to a course. Generally, it is a final inspection conducted prior to first use, and it ensures the new element or course was built to the designers’ specifications.
Structural Inspections
Not all operators realize that their annual third-party inspection is also typically a structural inspection focusing on chapter 1 of the ACCT “Design, Performance, and Inspection Standards.” A structural inspection looks at the state of your course and equipment on the day of inspection to ensure it is operating as intended and still meets standards.
Operational Reviews
An operational review is required every five years and should be conducted by a qualified person (per ACCT standard B.2.7.). Through firsthand assessment of a course’s operation, documentation such as manuals and forms, training procedures and processes, and component alignment, an operational review ensures a course is being operated as intended and and that it follows chapters 2 and 3 of the current ACCT standards.
If you follow a different standard, such as ASTM or PRCA, ensure you understand all components of that set of standards—not just a portion or chapter—as well as the requirements for operational reviews and/or audits. This is a great thing to discuss with the original manufacturer of your course, as well as your third-party inspector. —EM