When it comes to outfitting park staff—guides, maintenance workers, even those on the ground—equipment requirements differ from the gear worn by guests. The harnesses, lanyards, and helmets used by staff members must meet criteria and standards that are more attuned to some of the tasks unique to park staff.
There’s a lot to ponder when gearing up staff. The right equipment can help them enjoy their day while helping guests enjoy theirs, too. Three main areas to consider include: comfort, given that the gear might be worn continuously for several hours or more; performance, in allowing staff to conduct daily chores as well as emergency procedures; and worker safety, specifically in meeting local laws, regulations, and other industry standards.
OSHA and the Gang
Equipment sold in most markets should have a declaration of conformity indicated on the product or information in a manual or accompanying technical notice that shows what standards or ratings the item meets. This could be a marking that says “ANSI Z359.1” or “EN361” or “UIAA104”. These markings indicate that the manufacturer claims to meet these equipment standards—many of which are cited by regulators such as the Occupational Safety and Health Administration (OSHA) in the United States.
Meeting standards. Coming back to equipment selection, let’s take the last consideration first. OSHA is a body that sets criteria and requirements on equipment strengths, performance, and training for employers in the U.S. Many other organizations around the world also develop criteria for equipment, such as the International Climbing and Mountaineering Federation (UIAA) and the European Committee for Standardization (CEN).
These and many other organizations are also players in the standards game, each with various numbered sections in their codes that apply to standards for different gear or gear applications (e.g., harnesses, helmets, lanyards, and gloves). For operators in the United States, OSHA regulations and guidelines should be the principal concern, since those bear legal weight.
It’s important to note that most regulatory bodies like OSHA don’t write standards themselves. Rather, other organizations establish standards that can be followed to assure OSHA compliance. In its various regulations, OSHA frequently refers to standards from ANSI and others in guiding employers toward compliance. For example, in section 1926.100 of OSHA’s construction regulations covering head protection and fall protection, OSHA references ANSI Z89.1 as a guideline for determining the specifications for employee head protection.
Rohan Shahani, principal consultant at Redstone Solutions, points to the American Society of Safety Professionals (ASSP) ANSI Z359 Fall Protection Code as his preferred standard to meet most criteria set by OSHA and, in his home state of California, the California Division of Occupational Safety and Health (DOSH).
Check the checklist. To aid operators in achieving compliance with standards, OSHA creates industry-specific publications, such as the “Protecting Zip-Line Workers” pamphlet. Published in 2016, this handy guide briefly outlines the responsibilities employers have for workers at height. The checklist includes the types of gear guides must have, along with training, inspection, and maintenance requirements for gear and the workplace generally.
Equipment Specifics and Standards
Of course, there are many standards for different pieces of equipment, and there are many pieces of equipment able to meet these various standards and thus comply with OSHA regulations. Some items to consider:
Harnesses. Any employee working in an area where they are exposed to a fall should be equipped with an appropriate full body harness. There are many different harness styles as well as different standards and local requirements regarding harnesses, so operators should consult qualified persons to determine what the best harness will be for their staff to comply with all relevant laws and regulations, and more importantly, to best protect their staff from injury.
Helmets. For workers in the field where there’s a risk of impact or being hit in the head by falling objects, a helmet should be capable of cushioning blows to the top of the head, and ideally provide protection against side impacts as well. Ben Eaton of Petzl says a “sport” model with top-of-the-head protection but minimal side protection, like its Boreo helmet, might suffice for park guests, but a “professional” model like a Vertex or Strato, with better side protection and allowing for the attachment of accessories such as a face shield, makes more sense for guides.
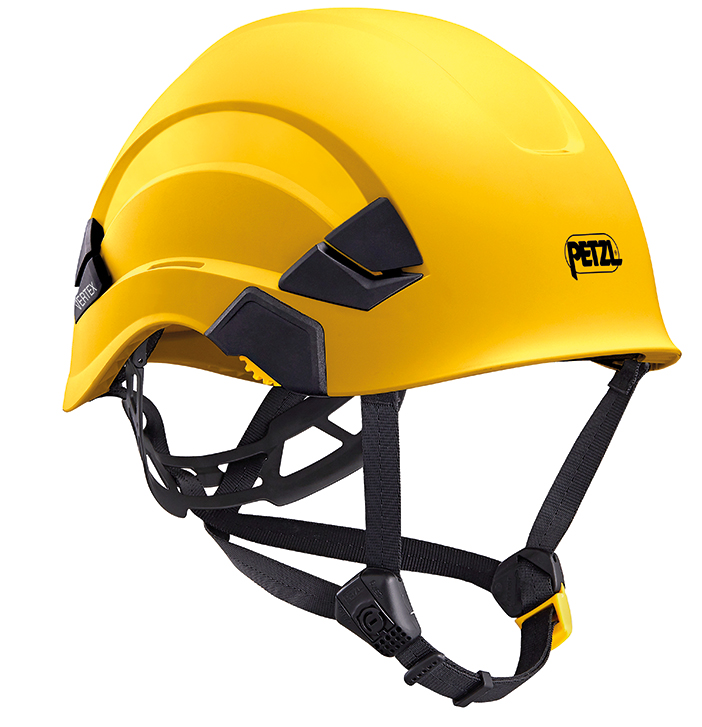
Professional-model helmets, like the Petzl Vertex, meet different needs than guest models.
Lanyards. Any lanyard must have a minimum breaking strength of 5,000 pounds.
Staying Up to Date
Ensuring that gear meets industry standards is up to equipment manufacturers, most of whom conduct rigorous testing before going to market. Equipment standards can have different criteria, be applicable in different areas, and sometimes even have different testing requirements, which may influence an operator to pick one product over another.
ROI. “Testing can be expensive,” says Shahani, “meaning that it can make a product more expensive.” While purchasing equipment for guides that meets some of these standards may cost more than similar consumer retail gear, the benefits of providing a high level of protection for employees—and avoiding possible lawsuits or OSHA violations—outweigh the extra dollars.
Slow to change. Staying up to date with the shifting sands of new regulations and standards may seem overwhelming, but in fact, change is rare and perpetually behind the curve. “Standards tend to change slowly and are not necessarily being evaluated to meet modern usage,” says Eaton.
Michael Johnson, CEO of Nature Outfitters, agrees. “Standards don’t change very frequently, and changes are usually minute things the equipment is already meeting,” he says.
As a general rule, laws change at a slower pace than equipment degrades, so it’s unlikely a piece of equipment will suddenly need to be replaced due to a new regulatory requirement.
Personal Choices
Standards aside, the responsibilities of individual guides—and how the equipment they use allows them to accomplish those tasks—will vary based on the size, design, and features of a park. There is a variety of gear each may carry during a workday.
Regardless, responsibility number one is guest safety.
Rescues and assists. For that reason, guides must be equipped with, or have access to, gear required for guest assists, rescues, and emergency procedures, whether carried on their body or accessible at strategic locations at the park. Bulkier rescue gear (i.e., cumbersome, heavy ropes) is best located where it can be easily accessed from various areas of the park, or near features where guest failure is most common or likely.
Exactly how a full rescue might be performed, and what equipment is needed, “depends a lot on the course and the belay system,” notes Johnson. One size does not necessarily fit all, especially regarding the variability of heights involved.
“For rescue procedures, there are a host of different systems out there, probably worth two or three articles,” says Shahani. For example, Petzl’s JAG system, for lowering a guest in a rescue procedure, comes with varying rope lengths, depending on the elevations involved. The DescendAll by Mark Save-A-Life is another example.
Lanyards and keyed systems. Full rescues, of course, are relatively rare, but assists—i.e., getting a guest dangling by a lanyard from the lifeline back into position on a particular feature—are more common. Experts typically recommend that guides use adjustable lanyards, allowing them to vary their elevation relative to the guest, making an assist much easier.
Guides at parks with keyed systems should carry an unlocking device, such as the tweezle key used with the LockD smart belay clips, so as to allow for a course lower if necessary.
Gloves. In addition, each guide should have a pair of gloves for handling the lifeline or sharp edges in case of an assist or rescue procedure. In fact, in its publication, “Protecting Zip-Line Workers,” OSHA says gloves could be among the safety gear operators “are responsible for providing” their employees working at height.
Comfort is a consideration that could easily get short shrift in choosing staff gear. However, as Alex Cox of adventure gear retailer Aerial Adventure Tech points out, “when staff are comfortable, you get more out of them.”
When it comes to comfort, the most important piece of equipment is the harness. Just how many comfort features are worthwhile and useful depends on variables including the size and configuration of a park, the nature of its features, the length of staff shifts, and how much time is spent in a suspended (i.e., full weight-bearing) position.
There are different considerations for staff vs. guest harnesses. For example, foam or padding at obvious pressure points, leg loops in particular, is a comfort feature that might be incorporated in a guide’s harness but would be extravagant in a guest’s harness. And easy adjustability, a good feature for guest harnesses, may be less of a concern for guides, especially if each has their own.
Who, When, Why?
Finally, there is the question of which employees need to be geared up in what equipment. Anyone working on course or at height, either as a guide or in performing maintenance tasks or emergency procedures, should be fully equipped with equipment that complies with applicable local regulations.
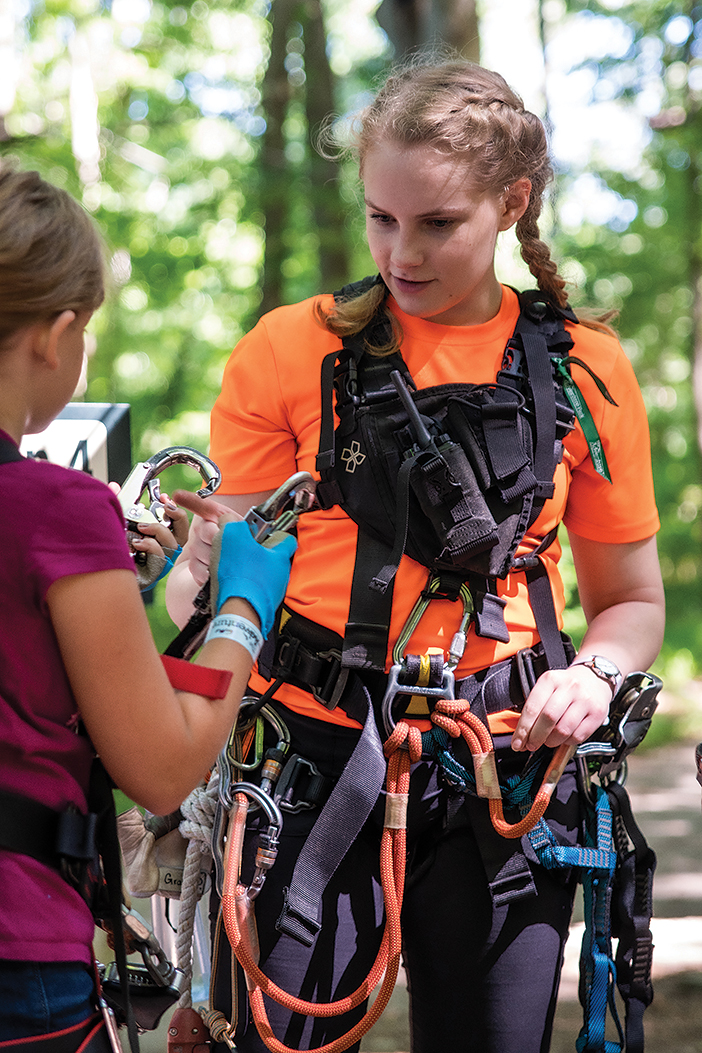
Gear worn by aerial park guides must meet specific standards in addition to the specific needs of the operation.
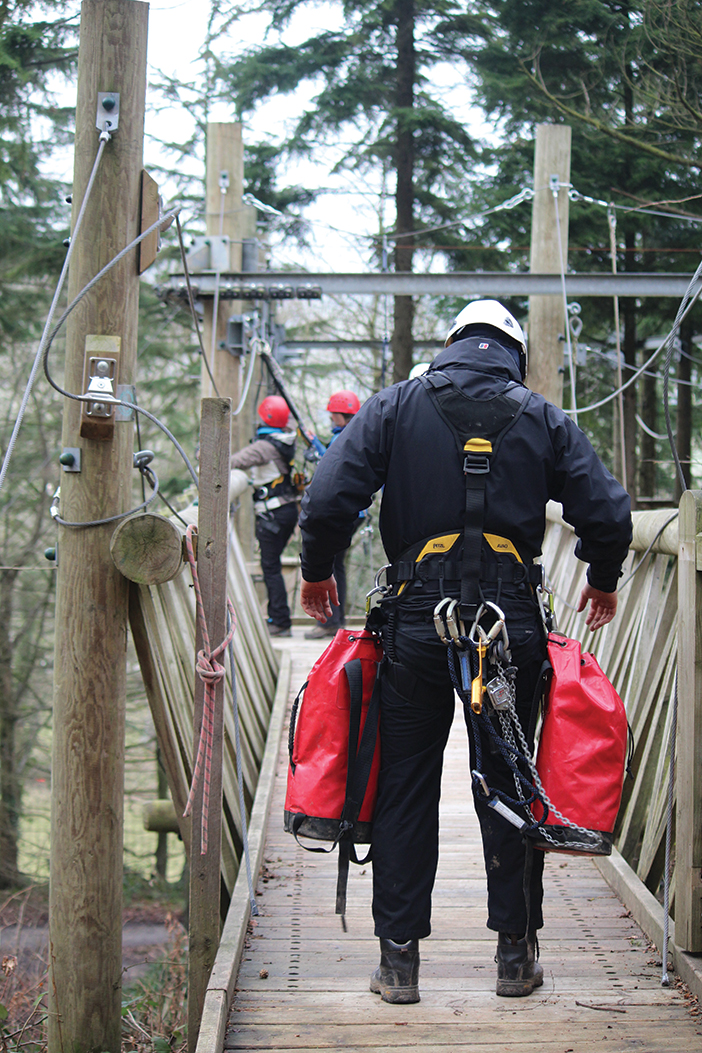
Rescue gear can be carried if it’s not too cumbersome, or positioned on-course at strategic locations.
But Shahani points out that they might not be the only employees exposed to potential workplace hazards. He suggests that any employee in an “operational” setting should don a helmet, a precaution he himself takes whenever visiting a park. Such a safety measure might not apply to, say, food-and-beverage employees or ticket sellers. But anyone who might have a remote chance of getting conked on the head would best be advised to wear a brain bucket.
Decisions, Decisions
Effectiveness, safety, and comfort all factor into the decision of how park operators should outfit their employees. While cost and compliance might get top priority when considering equipment, comfort and performance shouldn’t be overlooked. Getting the most out of operational employees means providing them with gear that fits well and is tailored to meet the specific needs presented by a park’s design. Simply put, it is worth spending a few extra dollars to be sure staff have the right gear—and the correct training in how to use it.