Zip line design is focused on going bigger, longer, and faster, and the task of keeping riders safe grows more complex. The popularity of zip lines continues to fuel growth in both quantity of operating sites and general volume of participants. That means the industry is faced with an escalation of risk. And that risk culminates in one small aspect of the zip line: the brake system.
It takes a carefully designed system, not just a well-designed device, to provide appropriate and safe zip line braking. This is a vital distinction that is fundamental to the safety of participants on a zip line, and helps start the conversation of why EADs (emergency brakes) have become such a hot topic in the industry.
It’s 3:00 a.m. and the sky is pitch black except for the neon lights reflecting off the clouds. My heart is in my throat and my mind is racing through checklist after checklist to make sure every item is in place. At this point, we have one task to complete: the EAD test.
Everyone has been cleared from the deck minus a few essential individuals, who are aware of and educated on the risks and potential consequences of this test. There’s tension in the air, a mixture of fear and anxious anticipation. I send out the command with almost instant regret, “Landing to launch deck, you are clear for launch on line one.” Now it is just a matter of waiting…
So, what is an EAD? The term is specific to zip lines and is an acronym for “Emergency Arrest Device.” These are also called backup brakes, secondary braking systems or assists, and emergency brakes.
The term first appeared as a brake-system product manufactured by Bonsai Designs and in the first Head Rush Technologies zipSTOP manual published circa March 2012. Both uses represent the same concept: an independent brake system designed to protect against operator error and third-party equipment failures. Head Rush also describes an EAD as an apparatus that stops a rider to prevent injury or death in instances where the primary brake does not perform as designed.
It’s hard to determine where the test dummy is when looking out over the zip line, with lights flashing and odd shadows being cast. We can finally see it when it’s about 500 feet out: a 300-pound test dummy hurtling toward us at 35 mph. The last couple hundred feet of cable bag the speed out a little, but we are still pushing 31 mph at arrival. This one is going to hurt. My shoulders tense up, I’m holding my breath, and I am conflicted between watching and looking away.
Of course, that impact is why this test is an absolute necessity. A bit of pain here (mostly for the test dummy) is worth the ability to sleep peacefully, knowing that no matter what, the guests on this zip line will be protected if the primary brake fails…
What do ACCT and ASTM have to say about EADs? That is what really matters at the end of the day, as the standards of these organizations have been, or are being, adopted by more and more jurisdictions.
WHAT ASTM SAYS
Within ASTM F2959-18, there are two applicable statements. First, it states that: “…If the failure of the braking systems results in an unsafe condition, then the braking system shall be fail-safe.” That means if the brake system can fail in any way, and the result is unsafe for the patron, then the ride (zip line) must have a fail-safe brake. This leaves us in a bit of limbo, because that definition never says EAD or anything even close. Perhaps the following line from ASTM will help a bit:
“Brakes shall be selected and designed to meet the needs of the aerial adventure course analysis and perform as required under any designer/engineer specified conditions and use.”
This adds more confusion to the conversation, because ASTM still does not mention EAD or any of its synonymous terms.
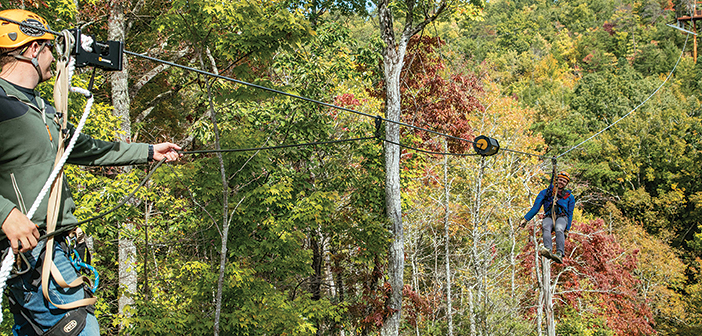
Hackwell Innovations’ Zipkea being used as the primary brake, and Autoprusik being used as the EAD.
Let’s break it down a bit. What is fail safe? ASTM provides a definition: “…component [of an amusement ride], that is designed such that the normal and expected failure mode results in a safe condition.” In other words, if everything fails in the way the designer has anticipated, the guest is still safe. Think of a gravity-stop zip line in that, outside of a catastrophic incident like an earthquake or gravity ceasing to exist, the guest is going to be just fine.
ASTM does not define or utilize the term EAD or its associated synonyms. However, it does state that it is the designer/engineer’s responsibility to determine an appropriate deceleration system by performing a failure analysis. This is a document describing every possible failure within the ride, the result of all such failures, and what the designer/engineer has done to mitigate the risk of the failure or prevent unsafe conditions resulting from it.
It is within this failure analysis that a designer/engineer will most likely determine that the main brake system can, in fact, fail, and that an independent, second brake system is required to provide safe braking conditions in the case of a failure.
WHAT ACCT SAYS
What about the Association for Challenge Course Technology (ACCT) standard? It is, after all, arguably more popular and prevalent in North America right now. Fortunately, this one is a bit more straightforward. The ACCT standard requires that an emergency brake be completely separate from the primary brake system or be an integrated backup feature of the primary brake. In addition, an emergency brake is required if the primary brake fails and “the participant arrives at the zip line landing area at a speed in excess of 6 mph (10 kph)” and “the participant experiences unintended and/or harmful contact with terrain, objects, or people in the zip line landing area.”
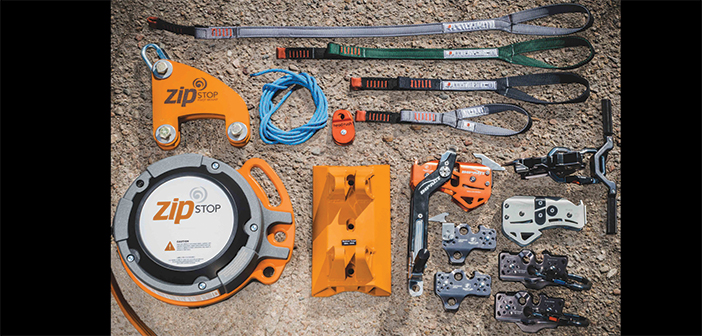
Complete Head Rush ZipSTOP system.
With these requirements, ACCT is plainly defining what an emergency brake is, what it must do, and how to determine when it is required.
Some jurisdictions have defined their own brake system criteria above and beyond the two existing standards. For example, Brian Lenihan of Clark County, Nev., explains that the County requires the manufacturer to “submit a test plan to evaluate the ride’s dynamic design characteristics to ensure safe performance,” and then perform independent tests of the primary brake and the EAD at the minimum and maximum ends of the design weight range, with accelerometers onboard the test dummies.
At the end, when all the tests and data have been compiled and analyzed, “Both systems must arrest the rider in a controlled safe manner without putting undue strain or forces on the rider,” or the ride fails.
To sum it up, ASTM and ACCT have very different approaches to the issue, but both agree on one key point: They require that brake systems bring the participant to a safe stop, even in the case of a complete primary brake failure.
After days and hours leading up to the test and then heightened seconds of nervous anticipation, the test dummy hurtles into the EAD at 31 mph. It’s not possible to convey the horrific noise of the EAD cycling above 100 percent; it was felt at the core of everyone in the direct vicinity. A massive sine wave shot up and down the zip line. My worst fears had been confirmed: The EAD was terribly insufficient. » cont.
Everyone on the deck silently exchanged looks; no one wanted to speak first. Yes, all the equipment held up, nothing was destroyed, and the test dummy was still intact—but the stopping force it experienced was well outside the allowable amount. We did not need an accelerometer to tell us the obvious. The test was probably survivable, but that was the best we could say about it…
IT STARTS WITH DESIGN
With dozens if not hundreds of builders, installers, designers, consultants, and engineers involved in the aerial adventure industry, there are many options for EAD systems, as well as many variables to consider when selecting an EAD. Valdo Lallemand, owner of Aerial Designs, lists five considerations—landing zone entry speed, zip line length, primary brake compatibility, manufacturer requirements, and landing deck length—as the most important variables in his company’s EAD design process. These variables help his team understand the energy that must be absorbed by the EAD, therefore allowing them to properly design a sufficient system.
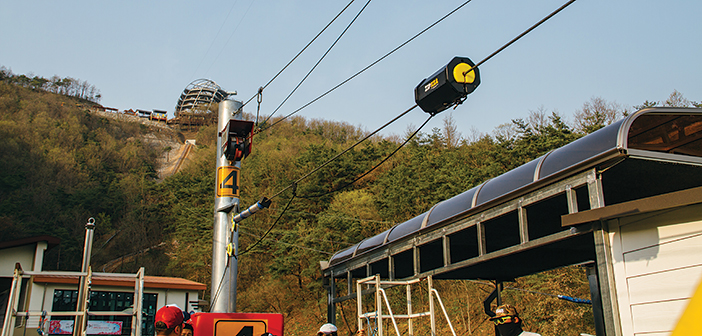
Hackwell Innovations Zipkea primary brake with spring brake EAD.
Understanding this energy, and designing specifically for it, are far more important than what Lallemand terms the traditional approach: designing for ease of operation, and then trying to design and implement an EAD that fits in.
POPULAR PRODUCTS
There are several popular options for EADs. Their suitability depends heavily on the characteristics of each particular zip line, so it’s essential to consult your designer/engineer on the systems prior to modifying your zip line.
Some choices include:
• Head Rush zipSTOP. This must be installed as a completely independent brake, meaning in normal operation, a guest must not activate it (this rings true for almost all EADs, but Head Rush is very serious about this). A testing program is provided and required.
• Spring Packs. Available from multiple manufacturers, springs are a very simple and reliable solution. The downside is the amount of space required for an acceptable brake.
• Bonsai EAD System. This is essentially a large cylindrical pad below the cable designed for impact. Must be used with Bonsai’s ecosystem of components, including trolley. A twin-line version is also available for dual cable systems. This system may require a manual reset, so it may not meet regulation requirements in all jurisdictions.
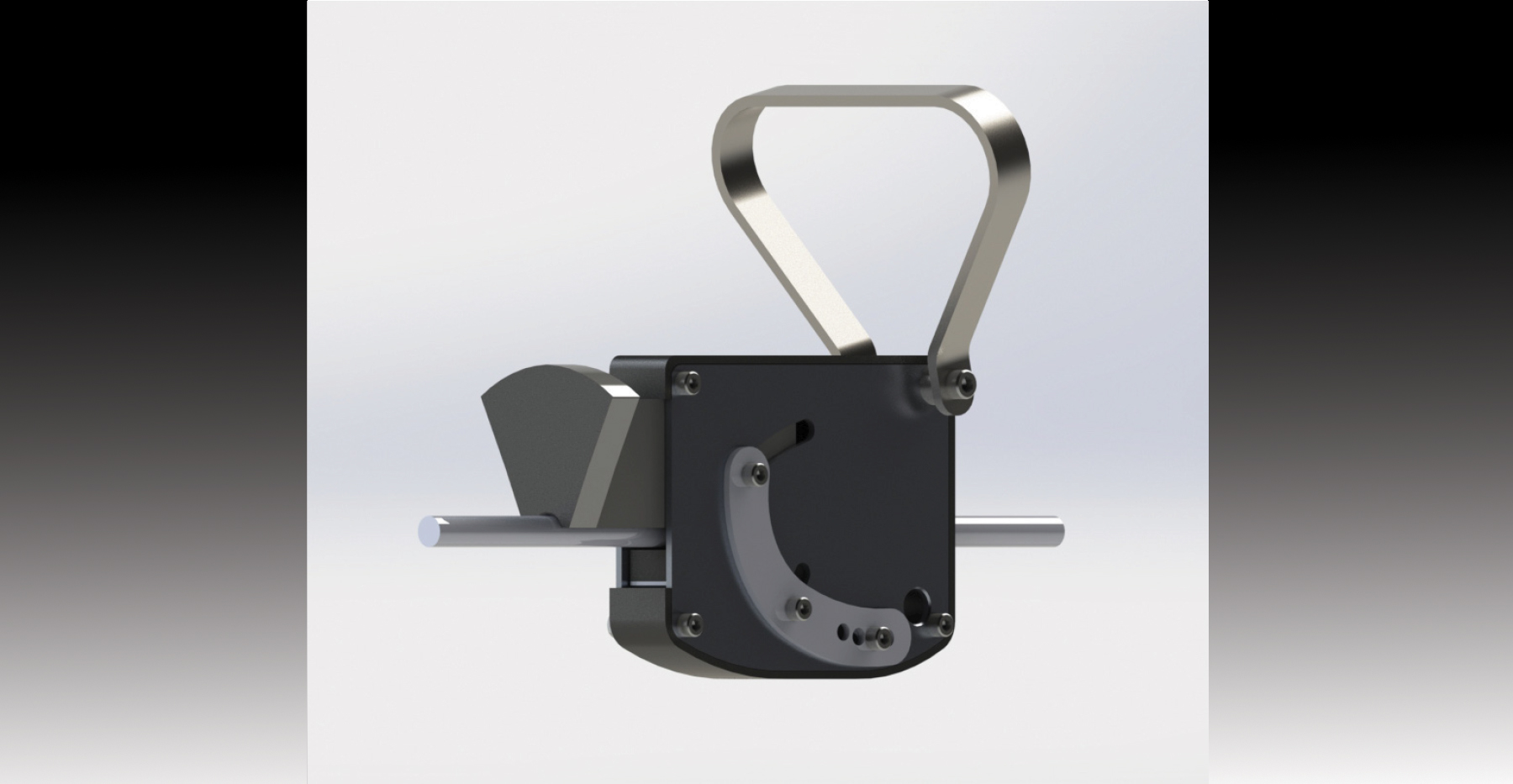
Bonsai Design’s Zip E-brake.
• Bonsai Zip E-Brake. Designed specifically for dual cable systems, the brake is activated independently from the primary brake system. An auto-reset option is available for install.
• Hackwell Innovations Zipkea. Like the zipSTOP solution, this is a redundant primary-brake-style EAD. The Zipkea, by design, requires a manual reset, so it may not meet regulation requirements in all jurisdictions.
• Prusik Knot or Hackwell Innovations Autoprusik. Normally recommended in more traditional setups for lower entry speeds, prusiks are often seen in canopy tours. Prusiks (and the Autoprusik) require a manual reset, so they may not meet regulation requirements in all jurisdictions.
• Gravity. This works every time! Gravity brakes are an example of a fail-safe brake system, but they must be designed for the purpose and tested accordingly. Generally, gravity systems are reserved for lower-throughput operations.
What’s best? Rich Reynolds of Head Rush Technologies believes that “The best EAD on the market is an EAD that has been tested on the zip line with the primary brake disengaged for the operational envelope (speed, weight, environmental conditions, etc.), and does not allow serious injuries on the participants.”
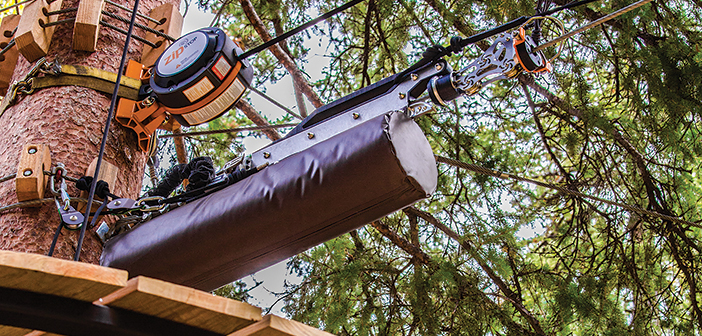
Bonsai Design’s single line EAD system coupled with a Head Rush zipSTOP primary brake.
That sums up the conversation well. There is no single perfect solution. Every installation is just a little bit different, so the needs can change across a vast range. Darryl Hore of Caliber Engineering notes that the spring pack option is a favorite within his firm when dealing with higher entry speeds, but the company recognizes this is not the ideal solution for every installation.
We went back to the drawing board, redesigned the EAD system, and re-tested a week later with all changes implemented. This time, though I was still filled with fear and anxious anticipation, I was far more confident in the system, because we had designed it with more facts and test data.
Once again, we were testing in the black of night, faced with the task of sending the test dummy down the zip line. My heart was still in my throat as the speed gun read 31 mph, the same as last time, and I began questioning every aspect of the system. This time, however, our work paid off and we came out with a very different result. Though the braking experience was rougher than the standard braking system, it was obvious on the video and in the data that we had a truly sufficient EAD. There was a collective sigh from everyone on the deck. We all knew we could finally rest easy and move forward with the ride …
HOW TO CHOOSE AN EAD
With all the various standards, regulations, options, and opinions, it can be difficult to decide on a solution and feel confident that your operation is making the best choice. Since there is no perfect product for every zip line (that I could find at least), here’s a guide to selecting the best EAD for your system so you can sleep at night knowing your guests have the greatest possible level of protection.
1. Talk with your designer/engineer. If you are unsure or uncomfortable with your current setup, contact a third-party company that specializes in your style of operation. ACCT’s PVM (Professional Vendor Member) program is a great way to prequalify companies, but there are many great independent consultants, too. Remember to check their references!
2. Talk to other operators who have installed the EADs you are considering. Get their honest opinion and feedback, not just a sales pitch.
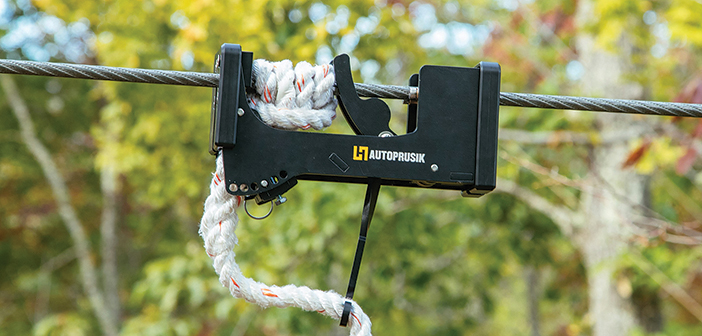
Hackwell Innovations Autoprusik EAD.
3. Verify a product’s use as an EAD with the device manufacturer. Make sure the implementation is within the intended scope, design, and operation of the device. Speeds, weights, and other operational parameters may limit use of some devices. This may also be relevant in systems utilizing off-the-shelf devices from related industries, such as an SRL (Self-Retracting Lifeline).
4. Test, test, test! This is where your fears will first max out and then be put to rest. It is important to follow the testing programs of the EAD device supplier and the ride manufacturer, assuming they have provided one. If one was not provided by either company, contact your designer/engineer to determine the best program for your site. Then, take videos and document these tests. This step is important for new and existing installations. If your primary braking system and EAD system were never tested and accompanied with documentation, it is wise to do so sooner rather than later.
5. Inspect and maintain your EADs in accordance with the requirements and recommendations provided by the device and zip line manufacturer(s). After spending all this time and money, you want to maintain your assets.